Awards and Commendations
- Top
- Business
- Powder Metallurgy
- Awards and Commendations
- Japan Powder Metallurgy Association
- Japan Society of Powder and Powder Metallurgy
The Japan Powder Metallurgy Association (JPMA) was founded on April 30, 1956, and currently has more than 70 member companies all over Japan which engage in manufacturing and sales of powder metallurgy products. The objective of the JPMA is to promote self-directed economic activity and to improve the economic status of its members by carrying out required business activities for the benefit of its members in the spirit of cooperation.
See more about the Japan Powder Metallurgy Association
JPMA Awards
The JPMA Awards were established in 1979 as a part of the promotion of the powder metallurgy industry.
The awards are divided into three categories: “Distinguished Service Award” for outstanding contribution to the JPMA business, “New Product Award” for outstanding powder metallurgy products, “New Powder Award” for outstanding raw material powders, and “Equipment Development Award” for outstanding manufacturing equipment.
The “New Product Award” is further divided into “New Design,” “New Material,” and “Process Development.” Since 2003, the “Grand Prix” has been given to especially excellent products selected by the selection committee. In addition, from among products that did not qualify for the awards, those with special characteristics are given an “Effort Prize.”
JPMA Awards given to Fine Sinter to date
- 2024
- 2023
- 2022
- 2021
- 2020
- 2019
- 2018
- 2017
- 2016
- 2015
- 2014
- 2013
- 2012
- 2011
- 2010
- 2009
- 2008
- 2007
- 2006
- 2005
- 2004
- 2003
- 2002
New Product Award, New Design
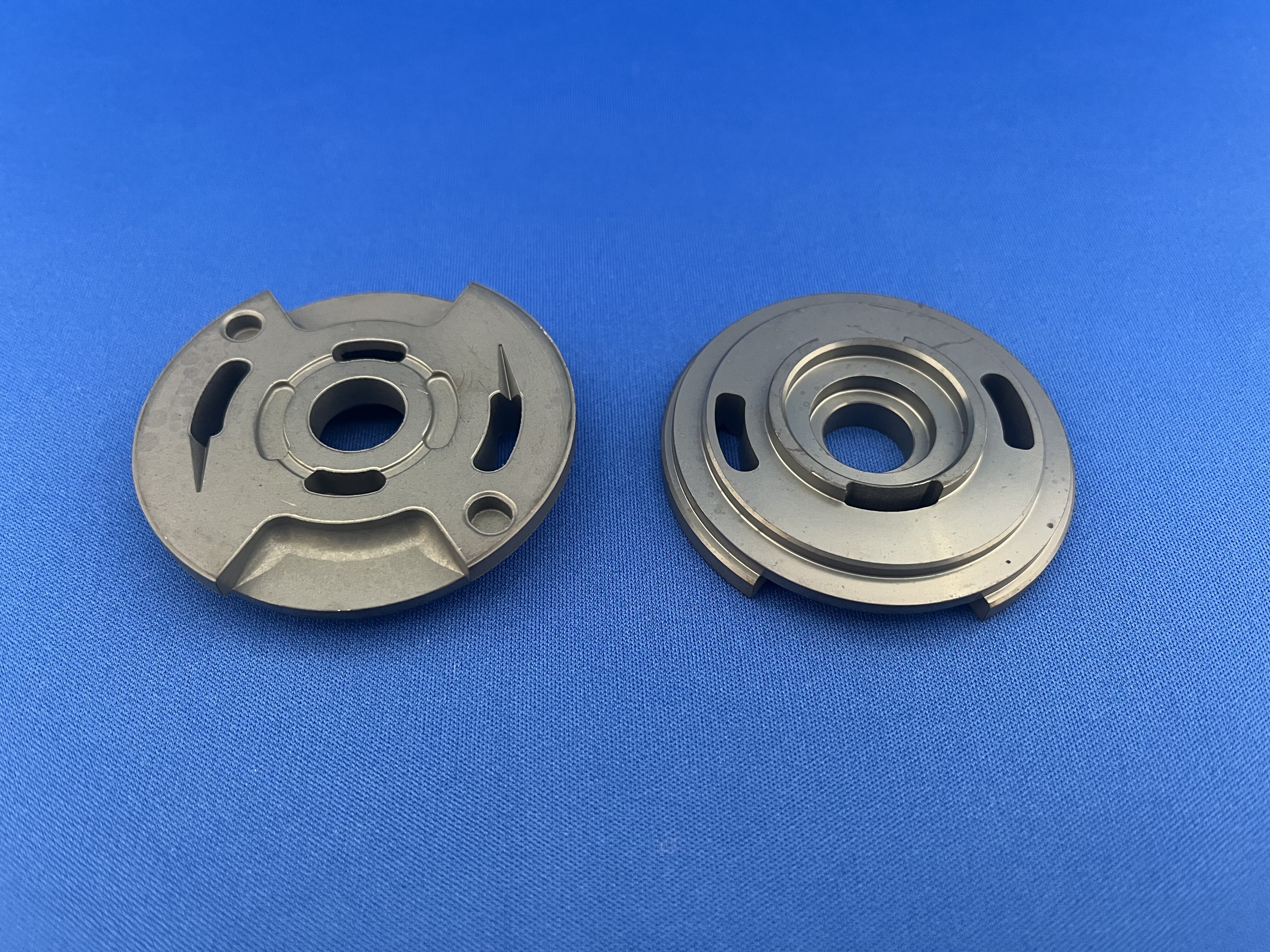
Vane Pump Side Plate Development with Molded Body Processing
The points appreciated are the fact that green machining of fine grooves is an extremely difficult technology, and that the ingenuity shown in optimizing the machining conditions. In addition, the green machining is recognized as one of the technologies that could potentially be important for the development of the PM industry, and for its potential to expand the scope of application of PM.
The green machining is expected to be applied to a variety of PM parts in the future.
Effort Prize
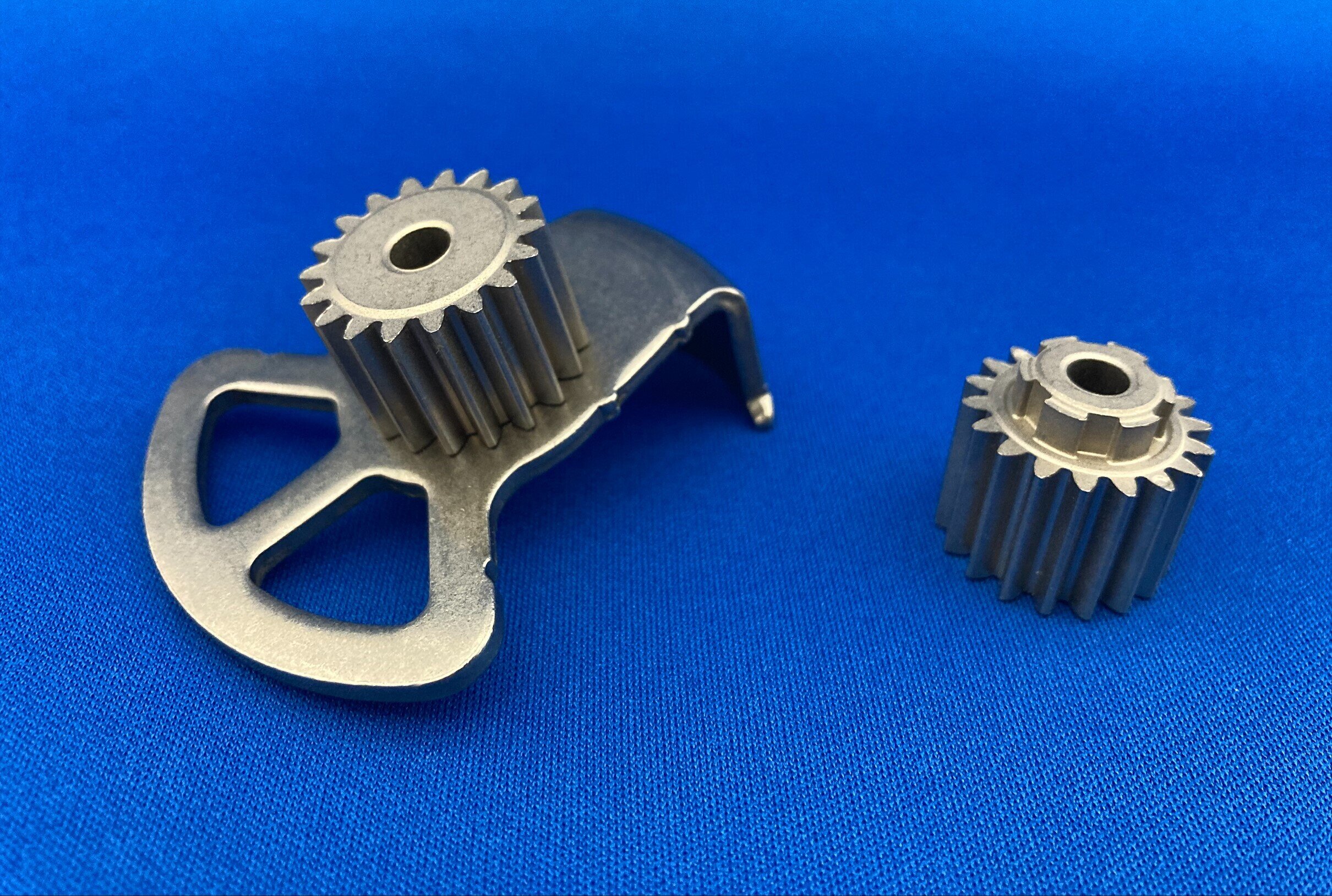
Sintered Actuator Components from the Development of Pressed Component Caulking Technology
The product was recognized for its combination of different materials, the plate and the sintered part, and for the unique ingenuity and design of the caulking joint. It is expected to be used not only in four-wheel drive parts, but also in applications such as connecting/disconnecting of power. The technology for joining different materials using plastic deforming processing was recognized as a reference example for PM industry with its contribution to the industry.
New Product Award, New Design
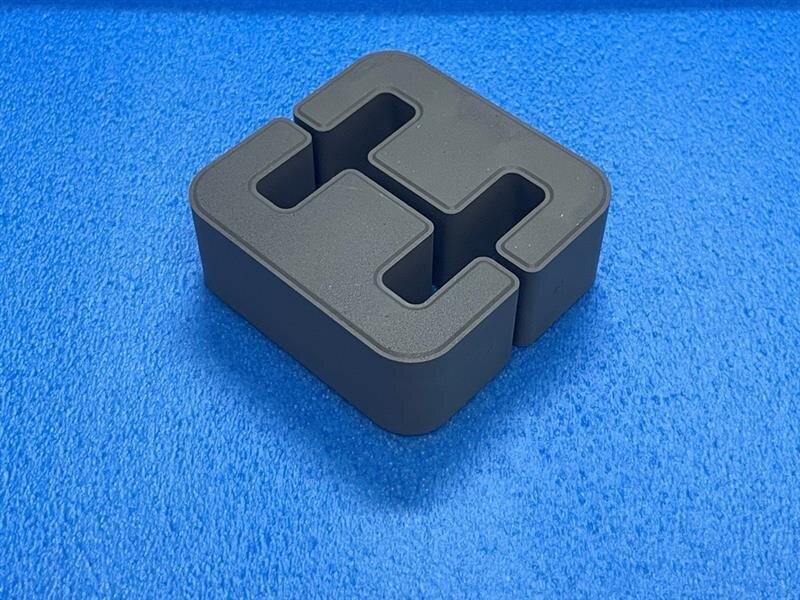
Practical Application of High Frequency & High Strength Reactor Core
The product was highly appreciated for its ability to reduce the product size by approximately 30% and the unit volume by 13% by developing a new material that overcomes conventional issues and significantly improving its properties. The product was also highly evaluated for its efforts to reduce product cost by approximately 30% through keeping improvement throughout the manufacturing process. This product is expected to be used more widely in electric systems, which are expected to continue to increase in the future.
New Product Award, New Design
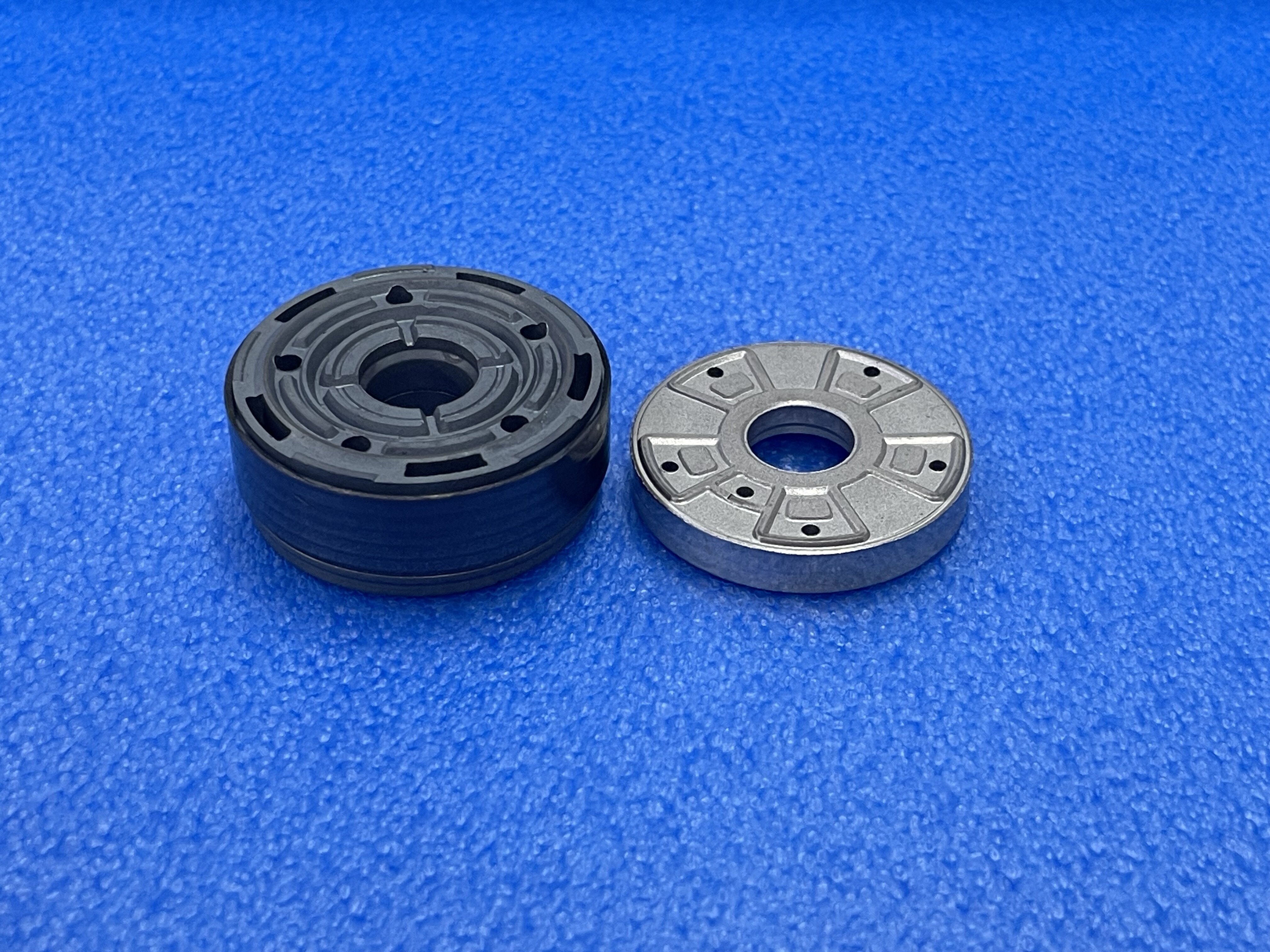
Development of high-precision parts for new mechanism semi-active suspension
Using advanced technology, the complex and high precision assembled parts that are difficult to achieve with competing manufacturing methods, were highly evaluated for meeting strict functional requirements and keeping cost control. This product is expected to continue to be in demand even as the electrification of vehicles progresses, and the technology is expected to be applied to similar parts.
New Product Award, New Design
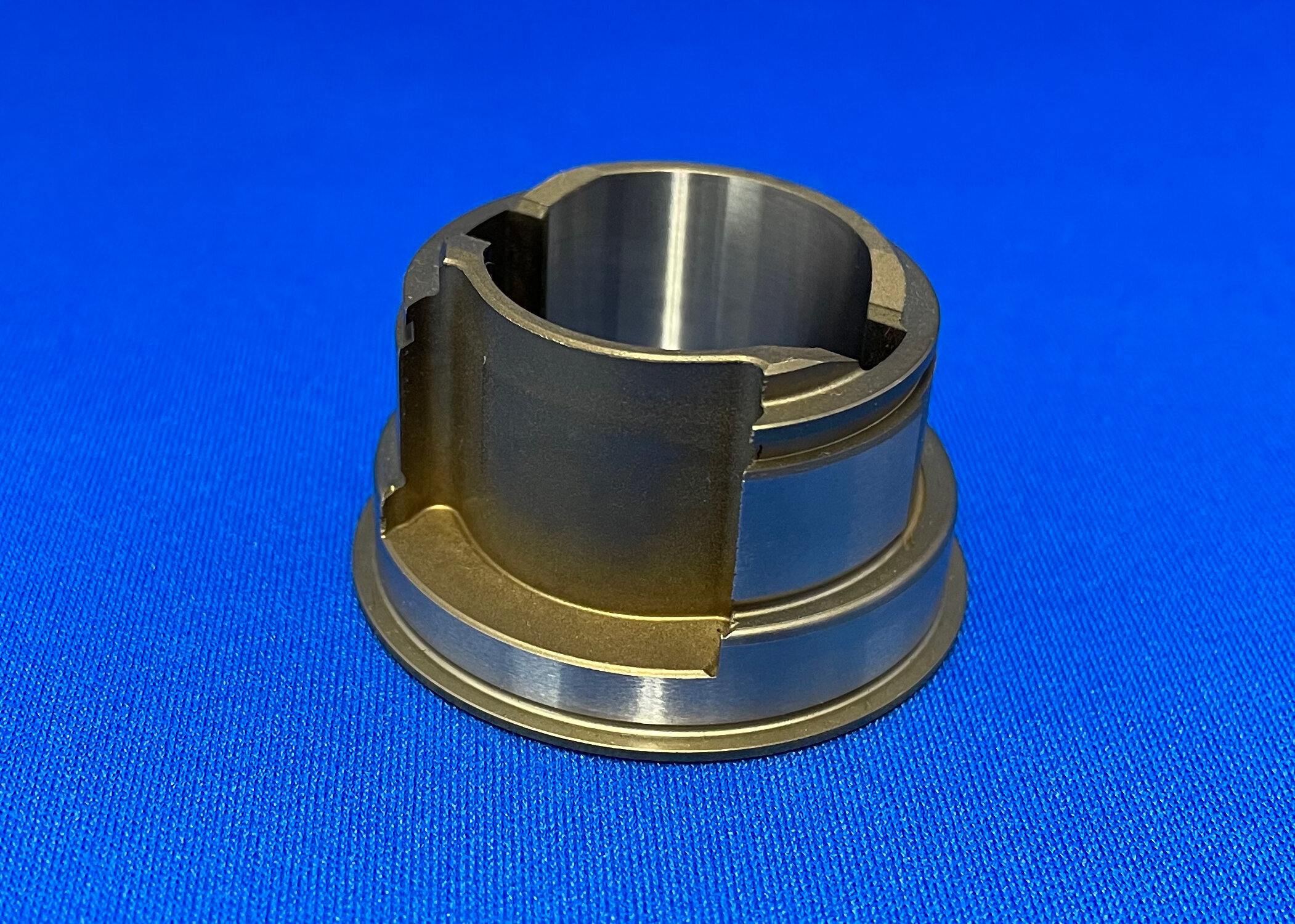
Mass production of high-precision thin-wall parts for electric VVT
The award was given in recognition of the technological expertise that fully utilized CAE analysis and achieved high precision for products with irregular shapes with thin walls that require hardening.
This technology is expected to expand the possibilities of powder metallurgy in the future, both in terms of solving difficult problems unique to sintering and in terms of product applications of electric VVT.
New Product Award, New Design
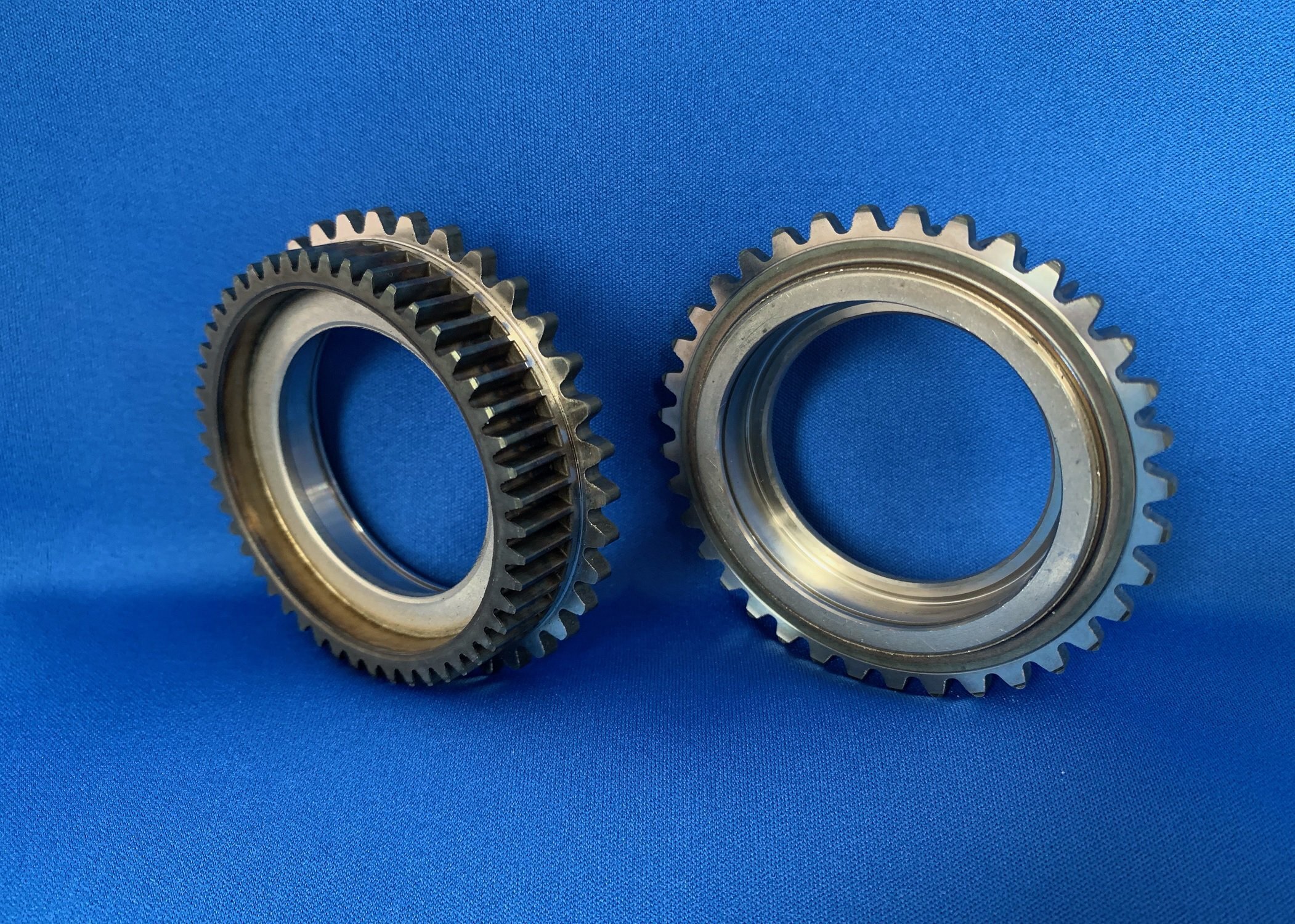
Development of sintered sprocket drive for one-motor hybrid vehicle
The award was given in recognition of the high comprehensive strength that brings together elemental technologies, such as improved forming processes supported by CAE analysis, optimization of single coil single shot induction hardening, and introduction of phrasing processes. Significant cost reductions compared to forging have been achieved and greater penetration into hybrid vehicles is expected.
New Product Award, New Material
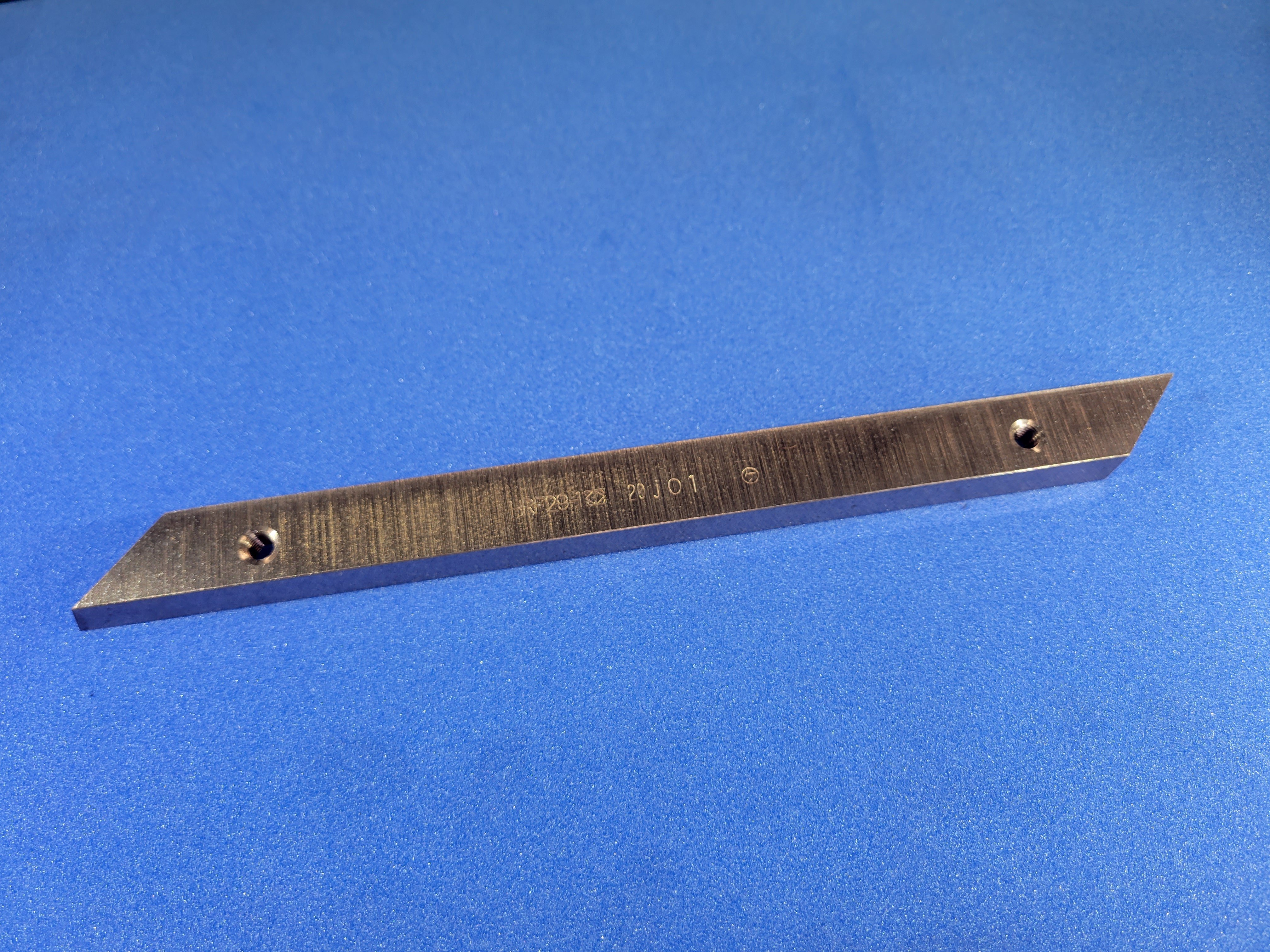
Development of copper-based sintered alloy contact strip with minimal trolley wire wear
The award was given in recognition of the development of a material that realized a balance between wear resistance of the contact strip itself and aggression to the trolley wire, which are required characteristics having a trade-off relationship, by optimizing hard particles, solid lubricants, and matrix. Actual train test results demonstrated significant improvement and sales expansion is expected in the future.
Effort Prize
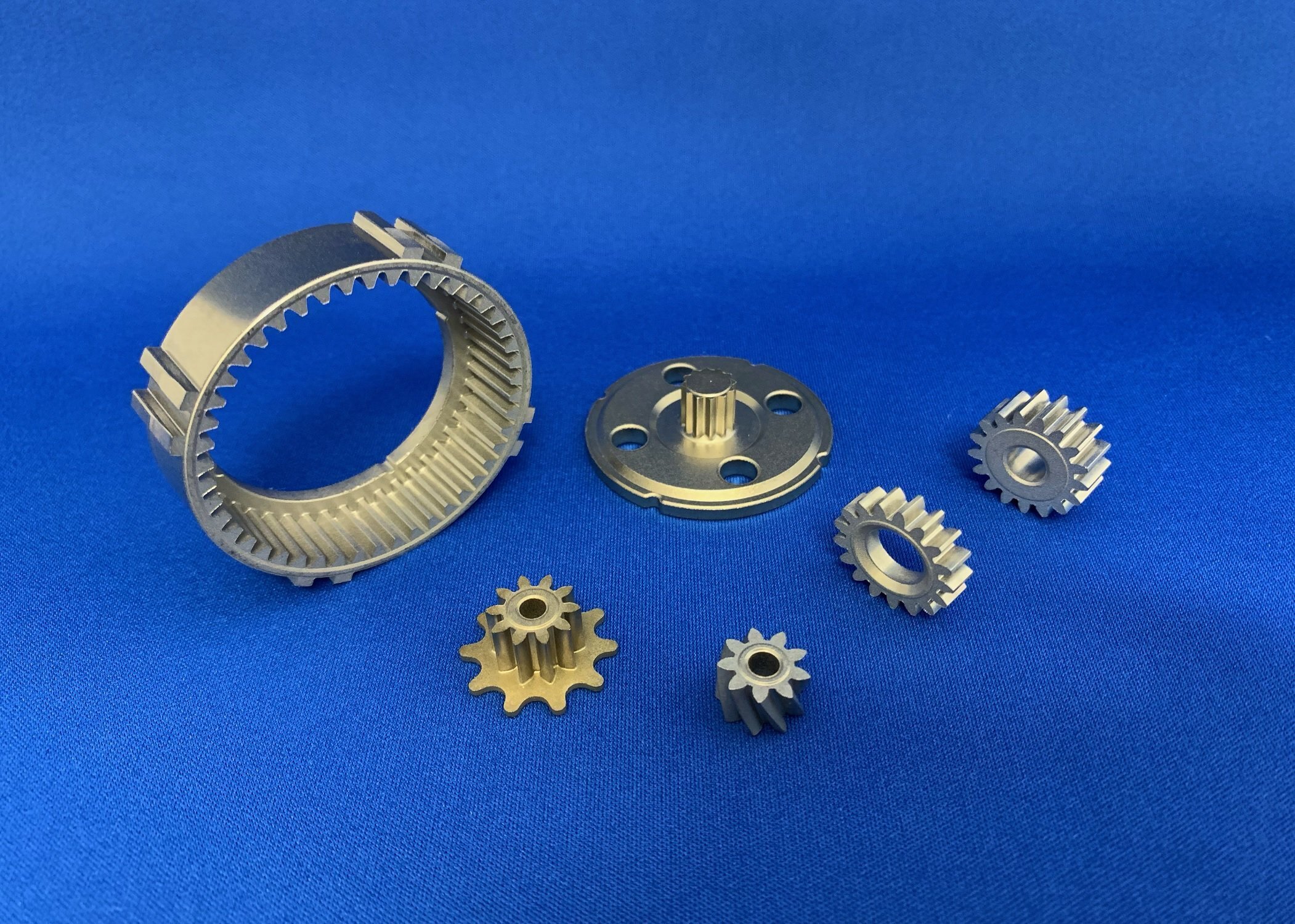
Adoption of sintered parts for EPB units of heavy-duty vehicles
The award was given in recognition of the combination of technologies that realized successful development and commercialization. In addition, the adoption for heavy-duty vehicles, where strength is required, is a good example demonstrating the superiority of sintered products.
New Product Award, New Design
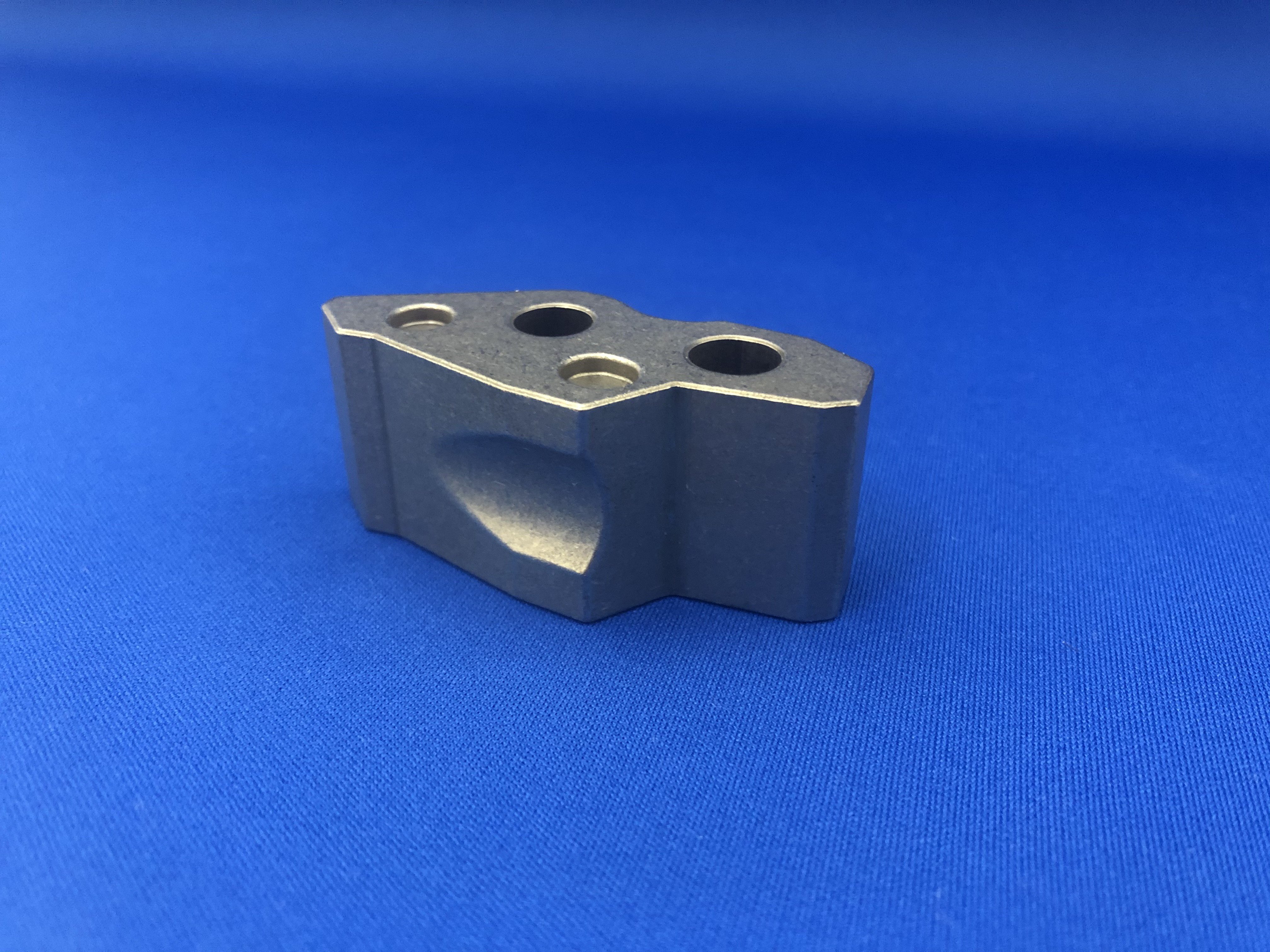
Cost reduction by making curvature grooves for parking lock parts using conventional press mechanism
The award was given in recognition of the realization of undercut compaction using a conventional press mechanism instead of a complicated mechanism, and the unique idea of localized die lubrication to prevent die galling. Wider use of a similar mechanism is expected.
Effort Prize
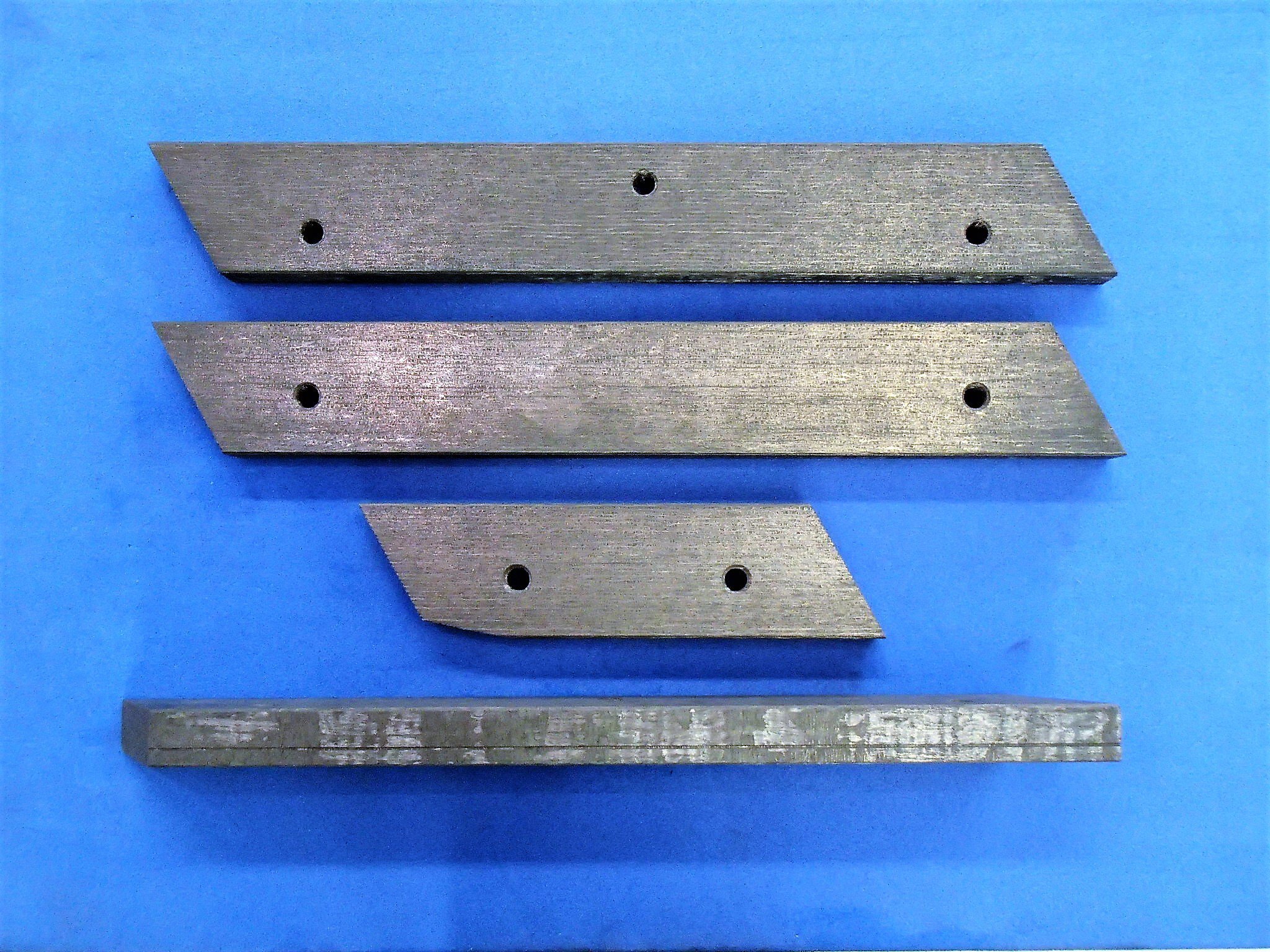
Development of lower cost C/C composite contact strip
The problem caused by reducing carbon fiber and increasing the binder was the decrease in the amount of infiltrated copper. The award was given in recognition of a solution to the problem by modifying the infiltrate and optimizing the infiltration technology as well as a successful reduction in the cost of the C/C composite contact strip, which was widely recognized as unique globally. This demonstrates the breadth of the market for sintered parts both domestically and internationally, and sales expansion is expected in the future.
Grand Prix
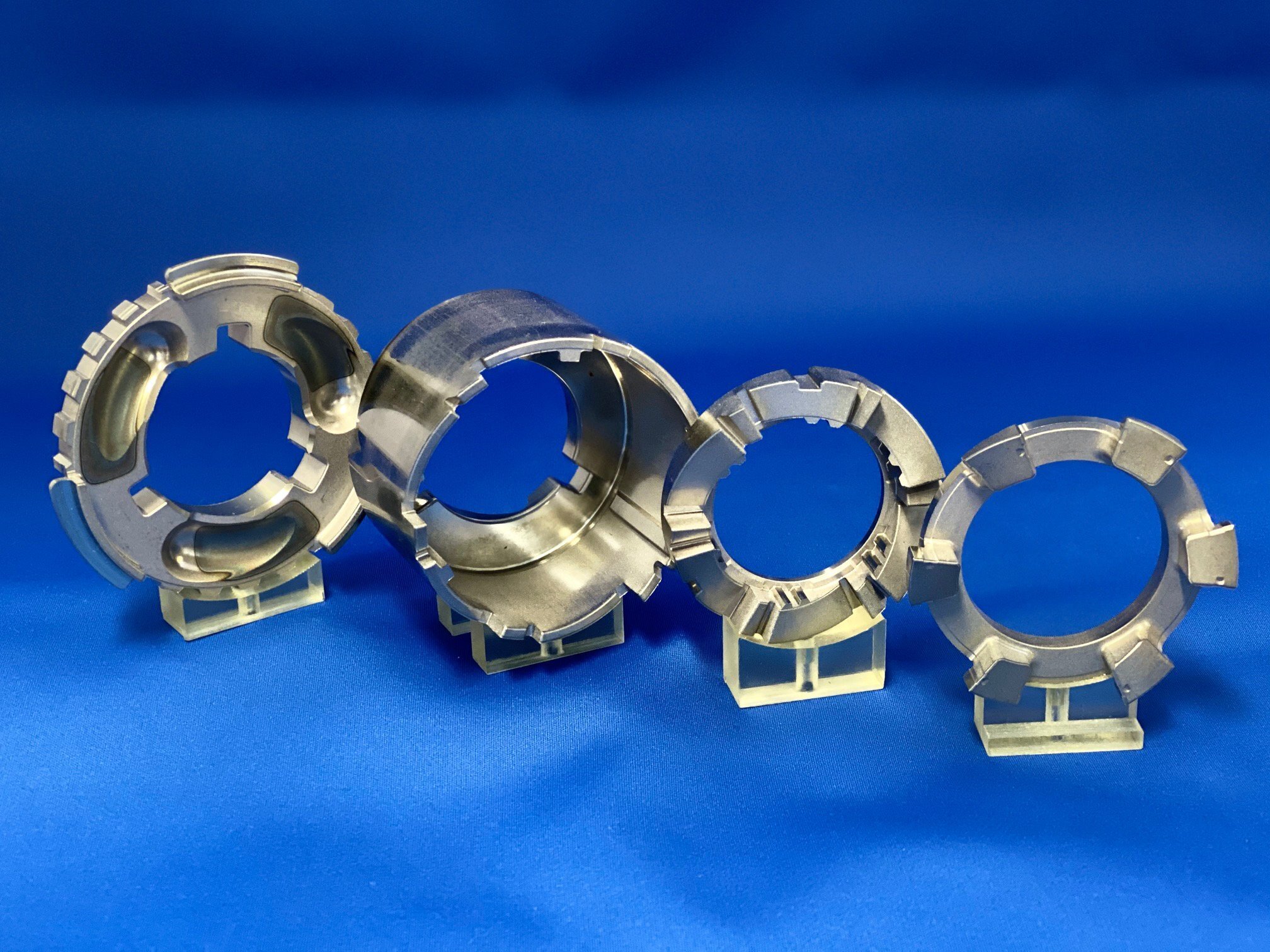
Technology & Development Award from Toyota Motor Corporation
Sintering of disconnect parts
Improving raw material powders and die structures enables compaction of ratchet shapes with large steps as well as thin-walled long shapes, and laser quenching of the waved ball groove end face ensures required characteristics. Realization of such parts with complex shapes that require a high level of technology was widely recognized. Such complex shapes tend to be avoided conventionally, however, the fact that mass production has been achieved through a number of countermeasures demonstrates the progress of near-net manufacturing technology for sintered products.
Further powder metallurgy market expansion is expected in the future by replacing other manufacturing processes.
New Product Award, New Design
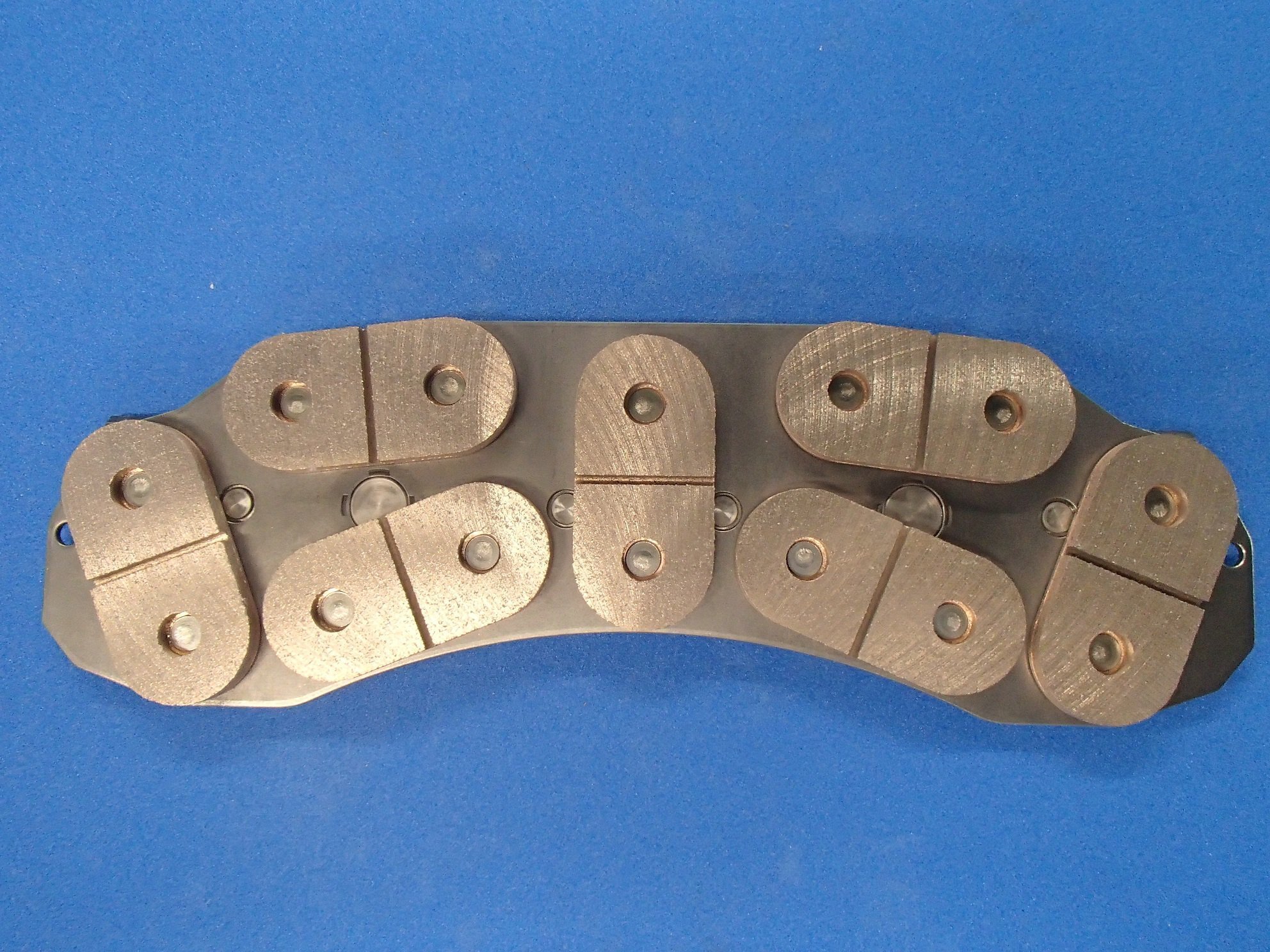
Sintered brake lining for new high-speed railway vehicles
Thanks to our unique equalizing contact pressure mechanism, we were able to improve the performance of the brake lining, including improved brake performance and wear resistance which contributes to safety and cost and received wide recognition for our achievement. In particular, the improved brake performance makes it possible to respond to emergency braking in the event of an earthquake, which was recognized as contributing to improving the safety of high-speed trains.
Market expansion for high-speed trains equipped with this brake lining is expected to expand in the future.
Effort Prize
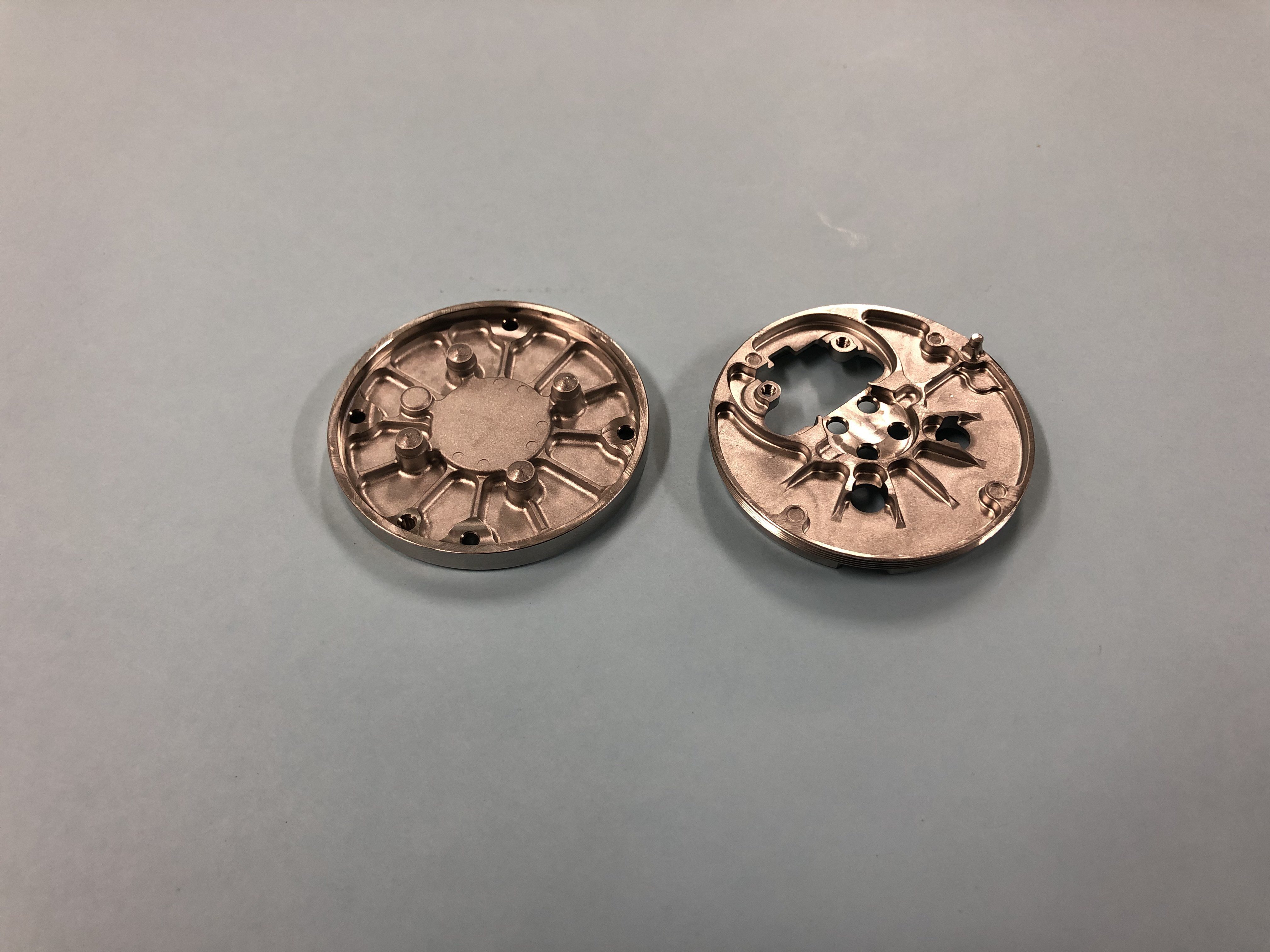
Cost reduction by using MIM to produce components for industrial collaborative robots
Product development that takes advantage of the characteristics of MIM was widely recognized for being adopted for industrial robots outside of the automotive industry. The cost reduction in the collaborative robot components contributed to lower robot prices, which in turn contributed to the promotion of global automation. This development is expected to provide a foothold for the development of new markets for powder metallurgy products, including small industrial robots.
New Product Award, New Design
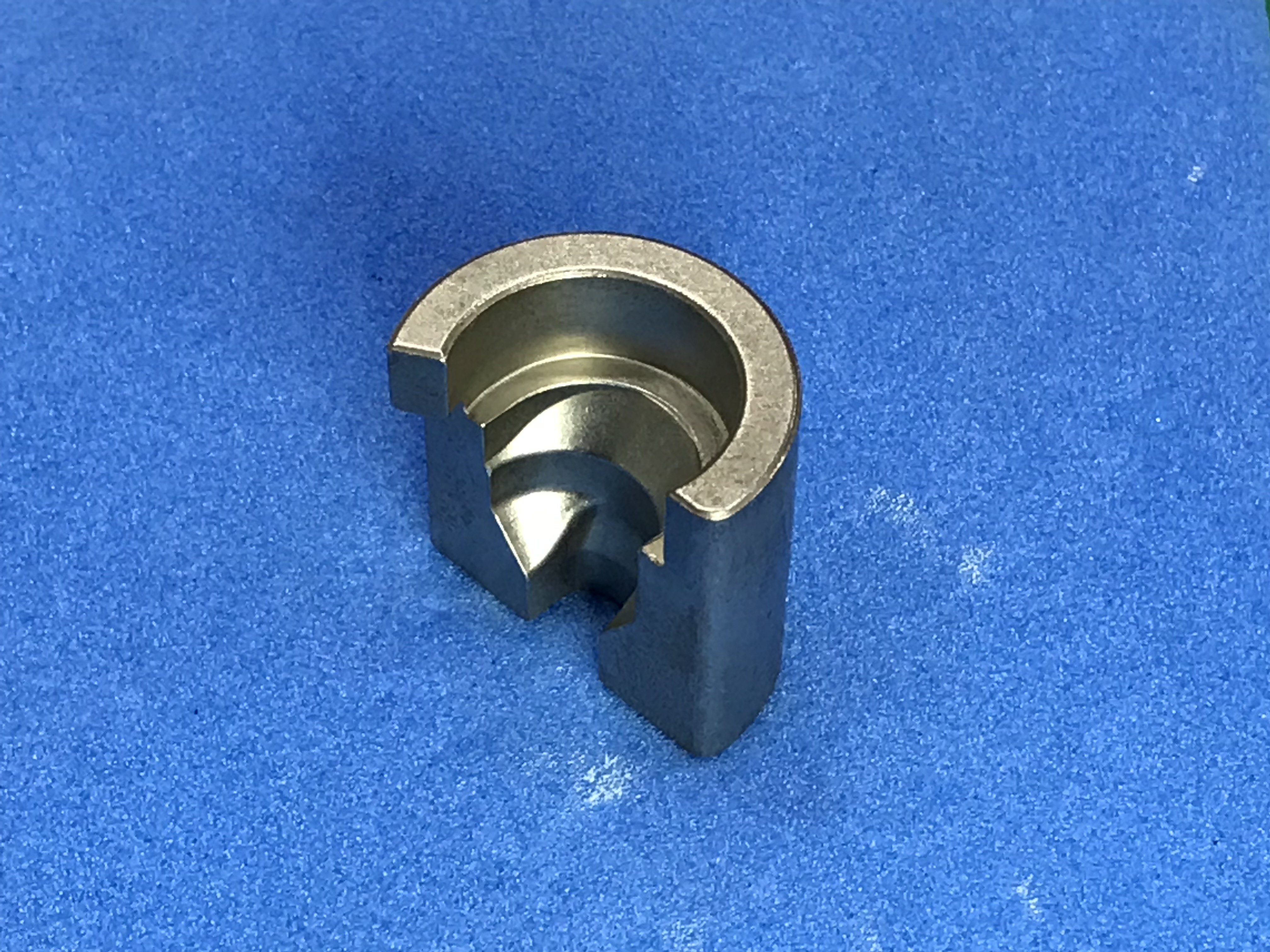
Driving part with multi-step taper shape for new-generation hybrid vehicles
We achieved multifunctionality of the product by realizing design-in and die structure improvements, and have received wide recognition for contributions to significant cost and weight reductions of user units.
This successful development demonstrated the superiority of sintered parts as parking lock parts for next-generation hybrid vehicles, and further market expansion is expected in the future.
New Product Award, New Design
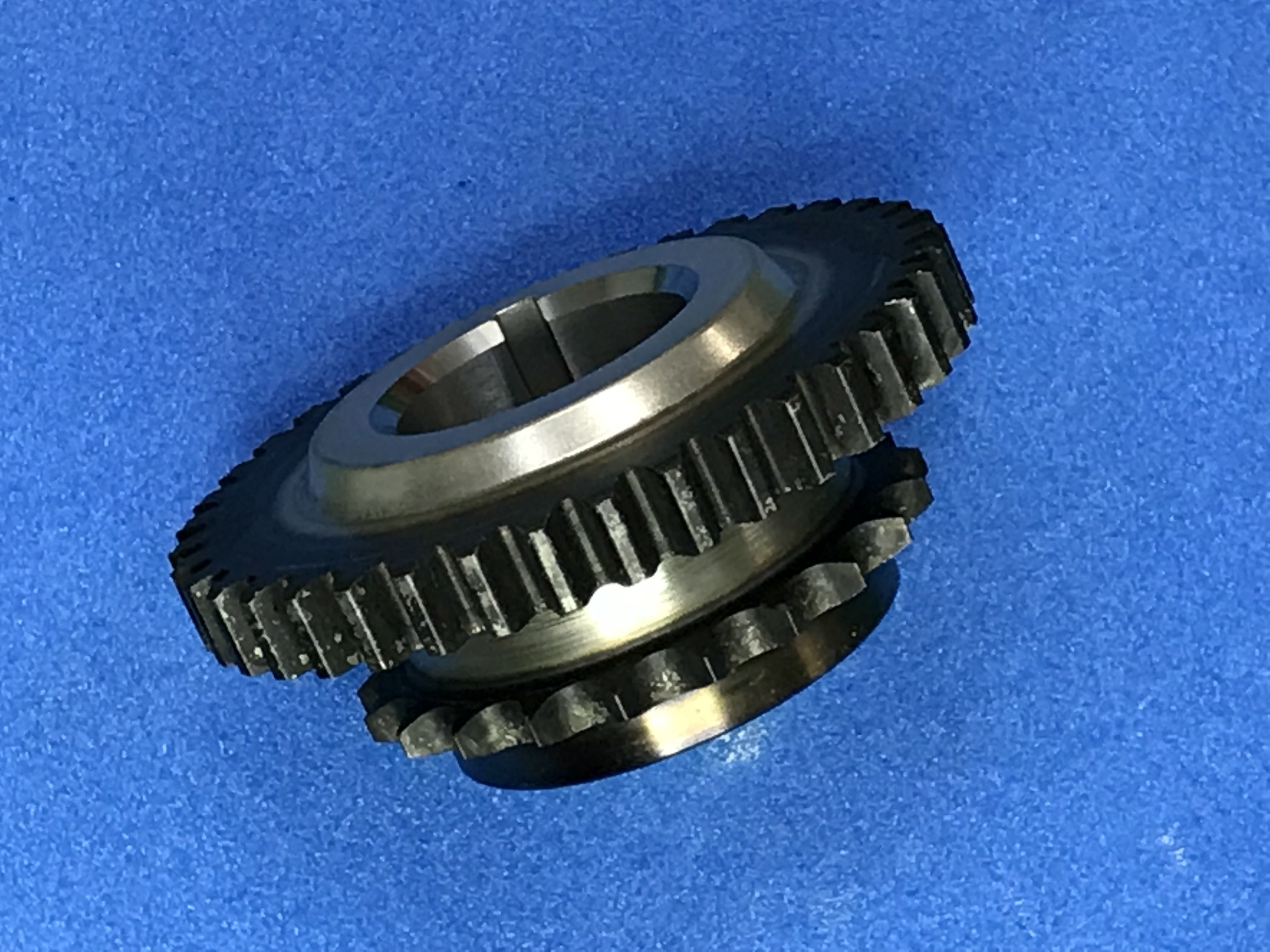
Low-cost high-density sprocket with die-lubrication less compaction
We received wide recognition for the realization of a density of 7.35 g/cm3 by conventional compaction and sintering in a mesh belt furnace, which reduced costs significantly. Such cost advantages over other manufacturing methods is expected to expand the market of powder metallurgy products in the future.
New Product Award, New Material Category
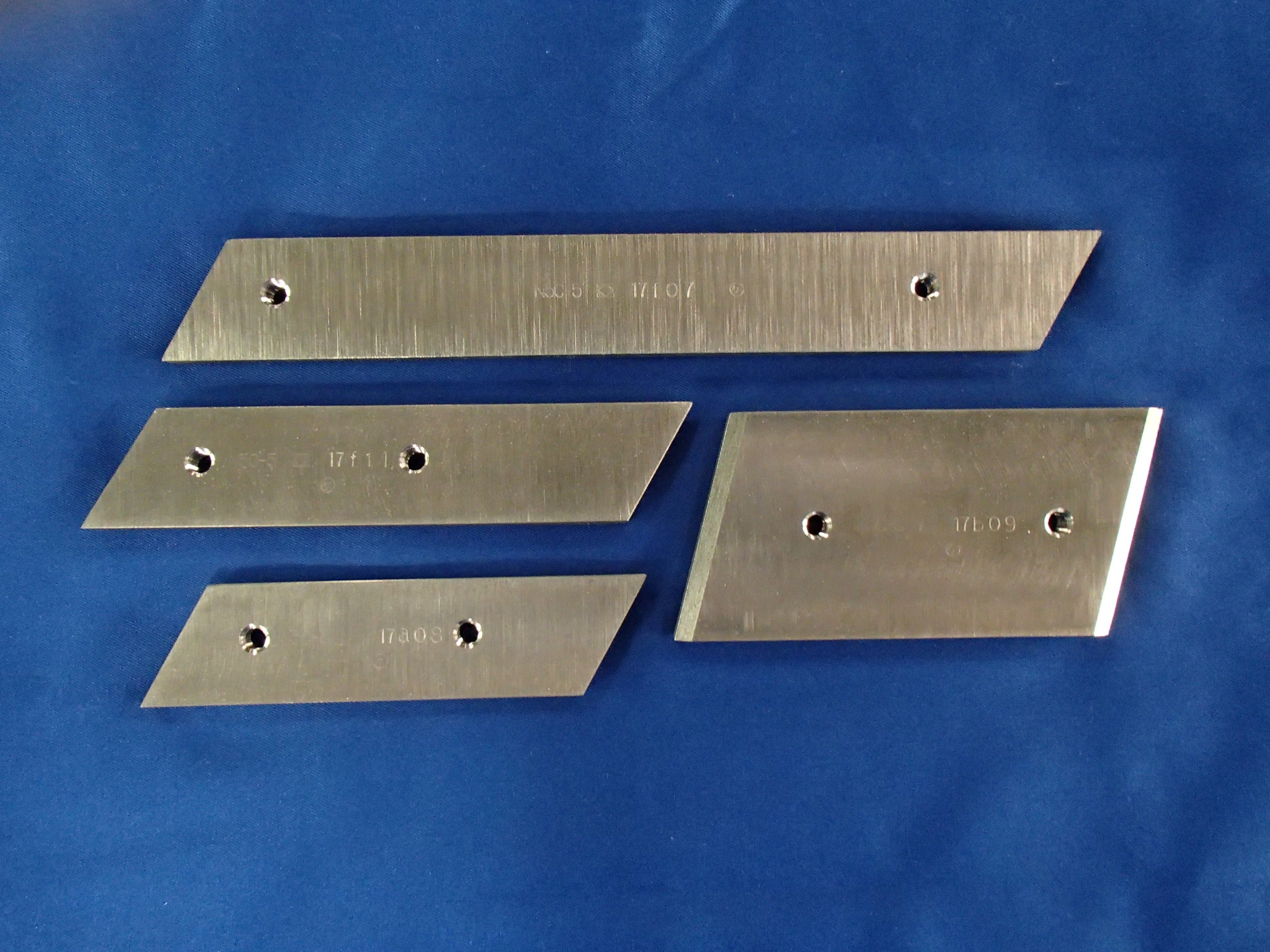
Highly wear-resistant Fe-based sintered alloy contact strip for high-speed trains
The award was given in recognition of the outstanding improvement in performance which realized about a 40% longer life compared with conventional products as well as a reduction in wear of the mating trolley wire. Since such characteristics can be achieved only with powder metallurgy at this time, this achievement is recognized as a contribution to the industry in terms of difficulty in switching to other technology.
New Product Award, New Material
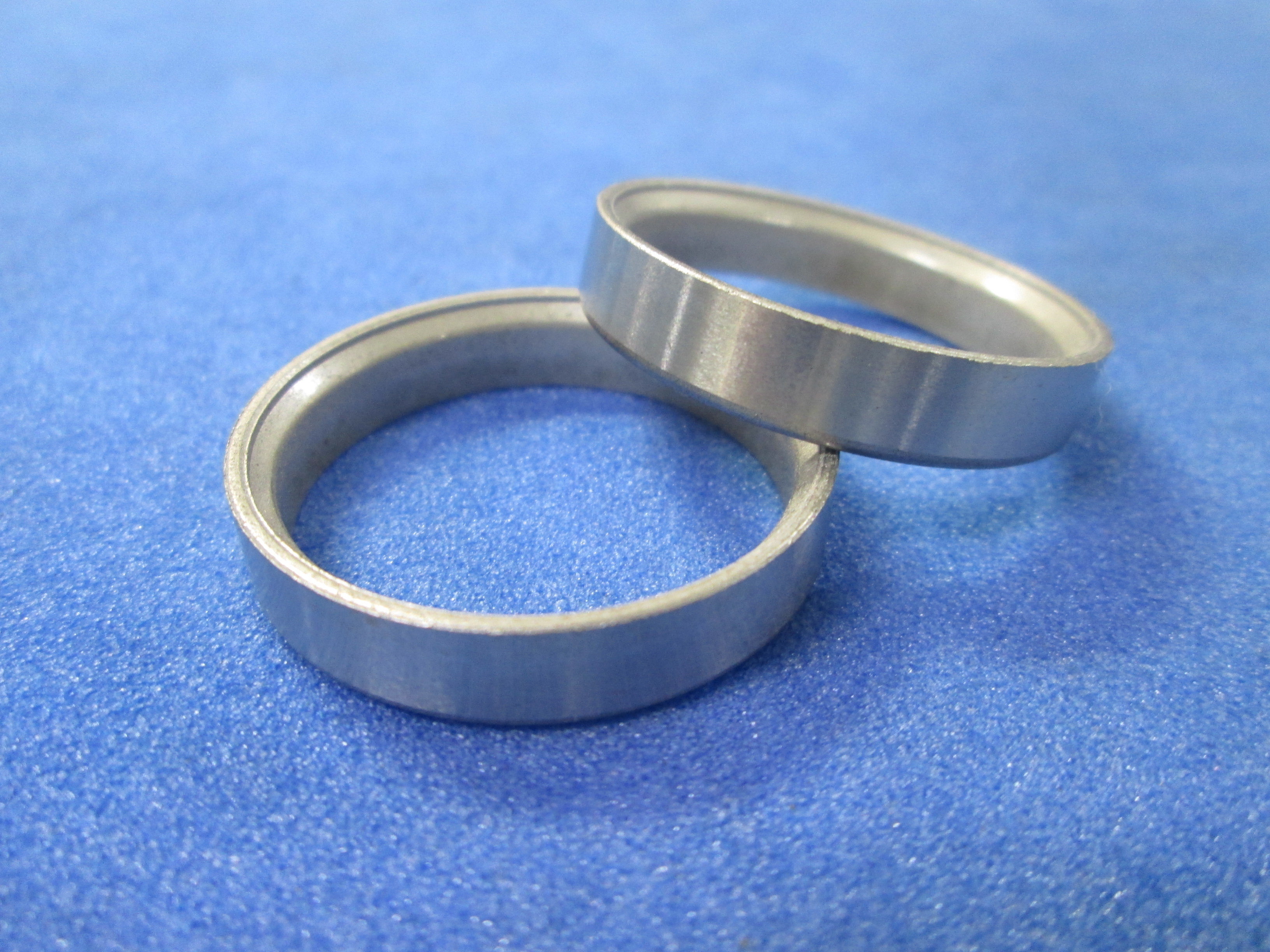
Matrix-toughened valve seat material with improved anti-adhesive wear resistance
It was through a novel and unique idea that the material was reinforced by dispersing micro fine hard particles in the matrix along with hard particles to improve anti-adhesive wear resistance. We received wide recognition for adding micro fine hard particles and greatly improving the quality and cost of the product, and its use in high-displacement, high-load engines has resulted in commercial production of 150,000 units/month, which is expected to lead to further development in the future.
New Product Award, New Design
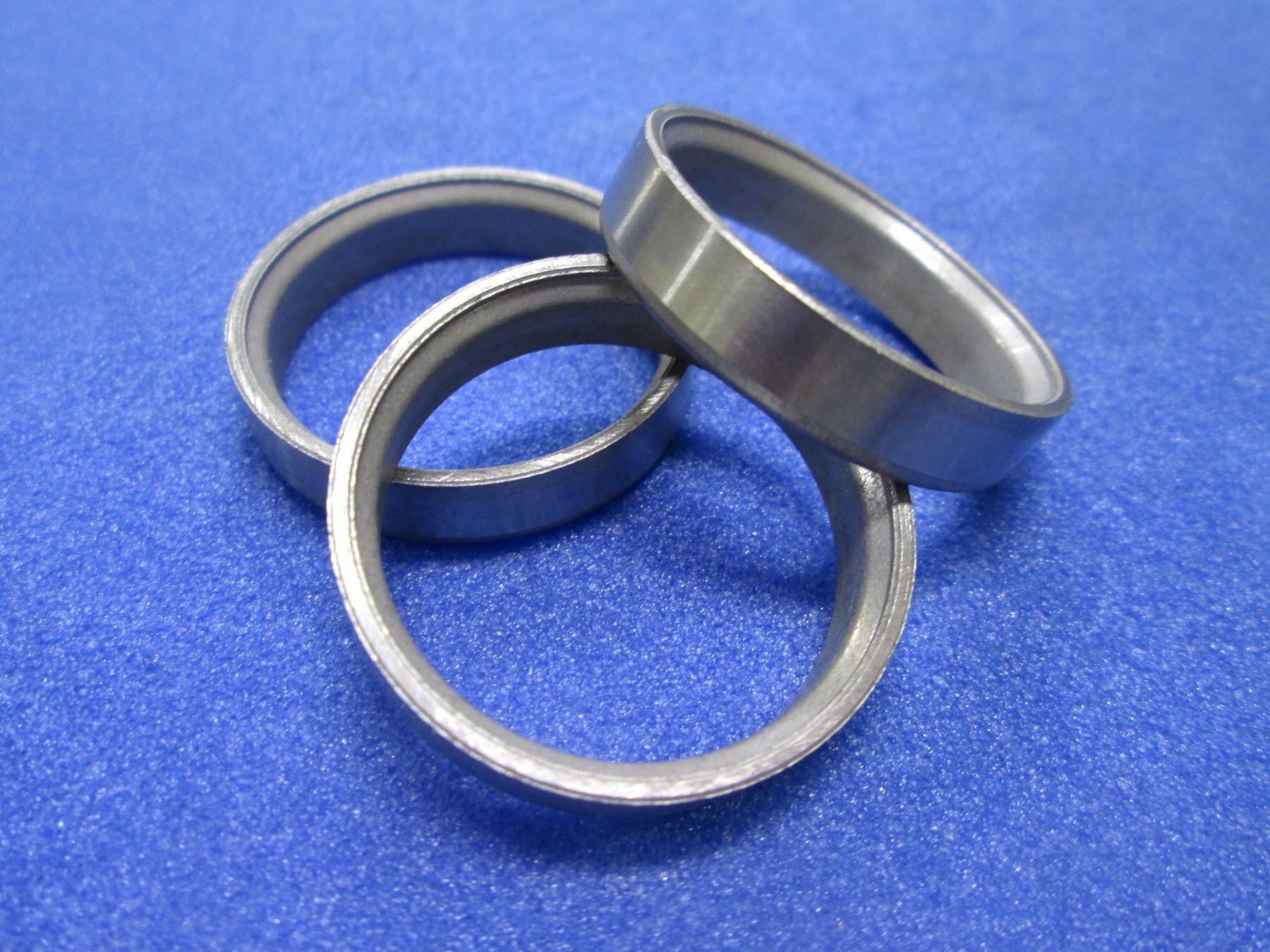
Higher cost performance by reducing wear resistant material of the valve seat by increasing the double-layer boundary angle
The award was given in recognition of the technological expertise to reduce high wear resistant material, achieving lower raw material cost, higher thermal conductivity, and improved machinability with no increase in production cost. In addition, the novelty and uniqueness of the double-layer forming technology with a boundary angle of 45 degrees and the possibility of application expansion in the future has also been widely recognized.
Equipment Development Award
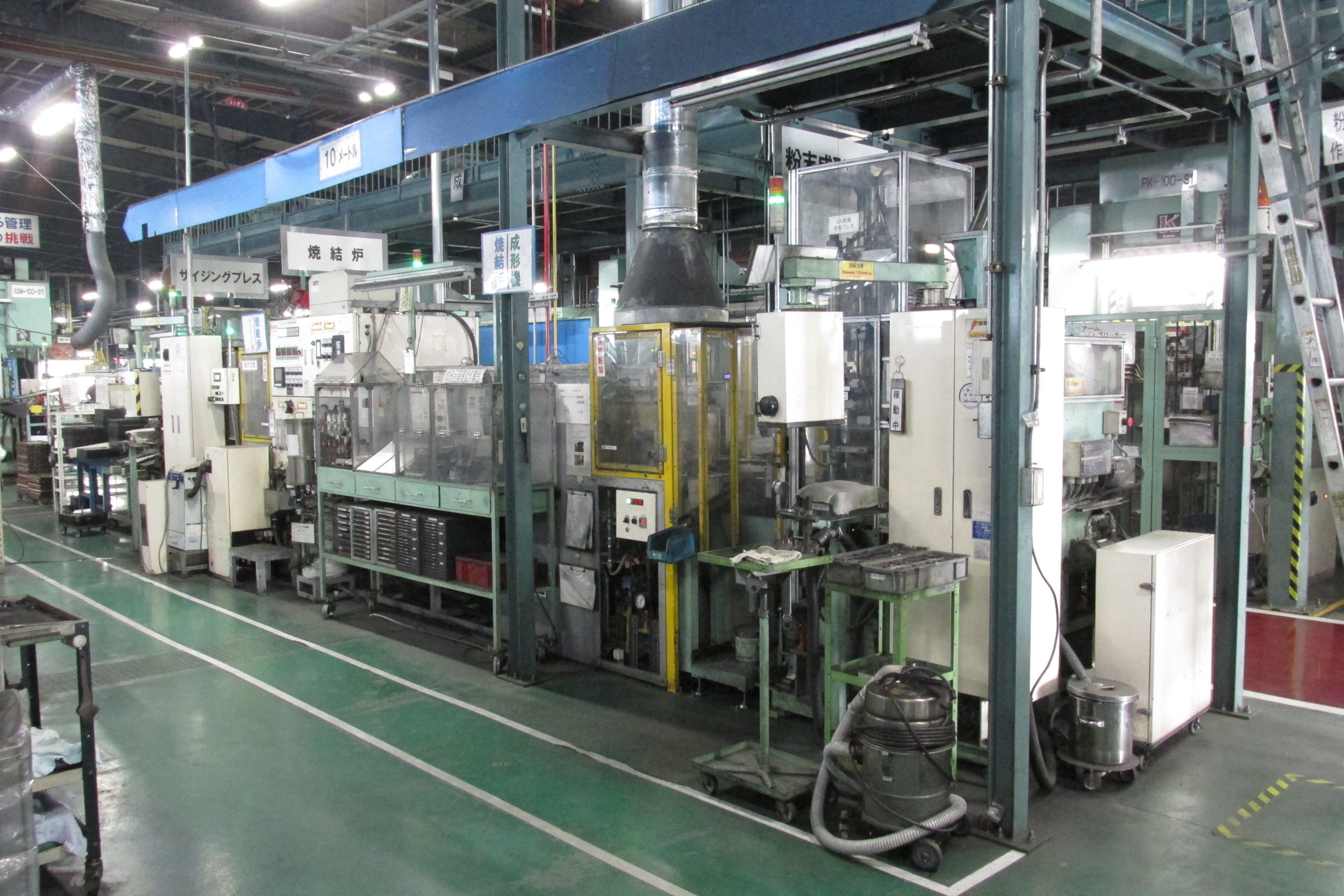
Compact integrated production line exclusive for shock absorber parts
The originality of the technology that made it possible to complete the total process time in 44 minutes from compacting to sizing, including shortening the sintering time, and the novelty of a compact production line were widely recognized.
Effort Prize
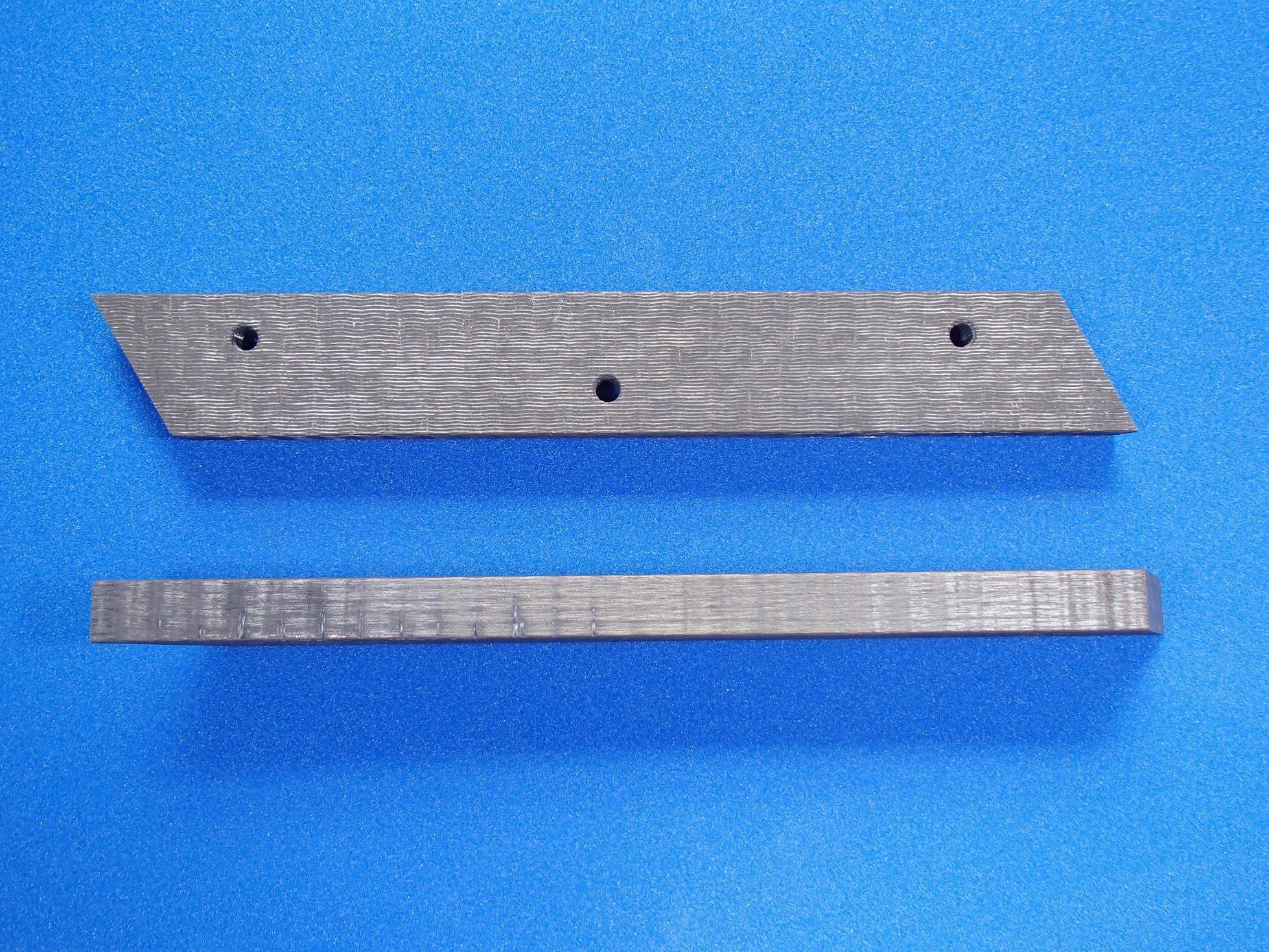
Sintered contact strip material made from C/C composite impregnated with copper alloy used for electric trains
This material is made from C/C composite and copper alloy by the complex powder metallurgy technology. With demand expected to expand overseas in the future, its contribution to the industry has been widely recognized.
New Product Award, New Design
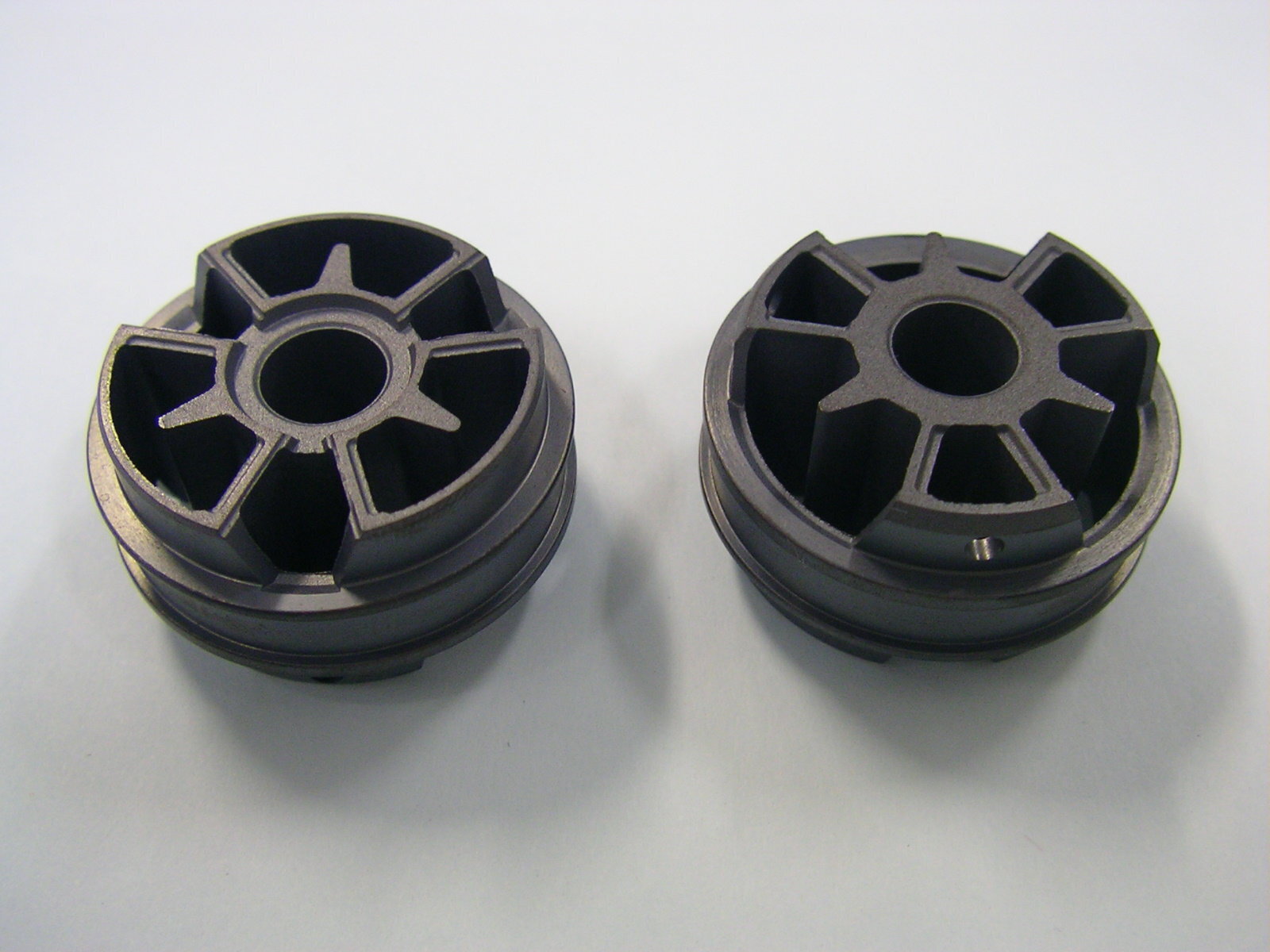
Mass production of thin-walled lightweight pistons for motorcycles
The ingenuity of the design and compaction method that enables complex shapes with thin-walled and concavo-convex sections were widely recognized. The contribution to the improvement of motorcycle performance, such as stabilization of damping force characteristics was also widely recognized.
Effort Prize
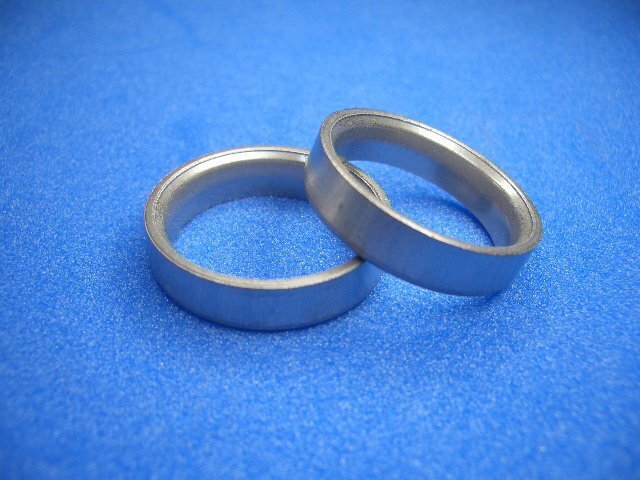
Valve seat material with hard particles of improved wear resistance
The novelty of the method to disperse oxides by adding rare earth metals, the reduction in material costs, and the potential for use in other valve seat materials were widely recognized.
Effort Prize
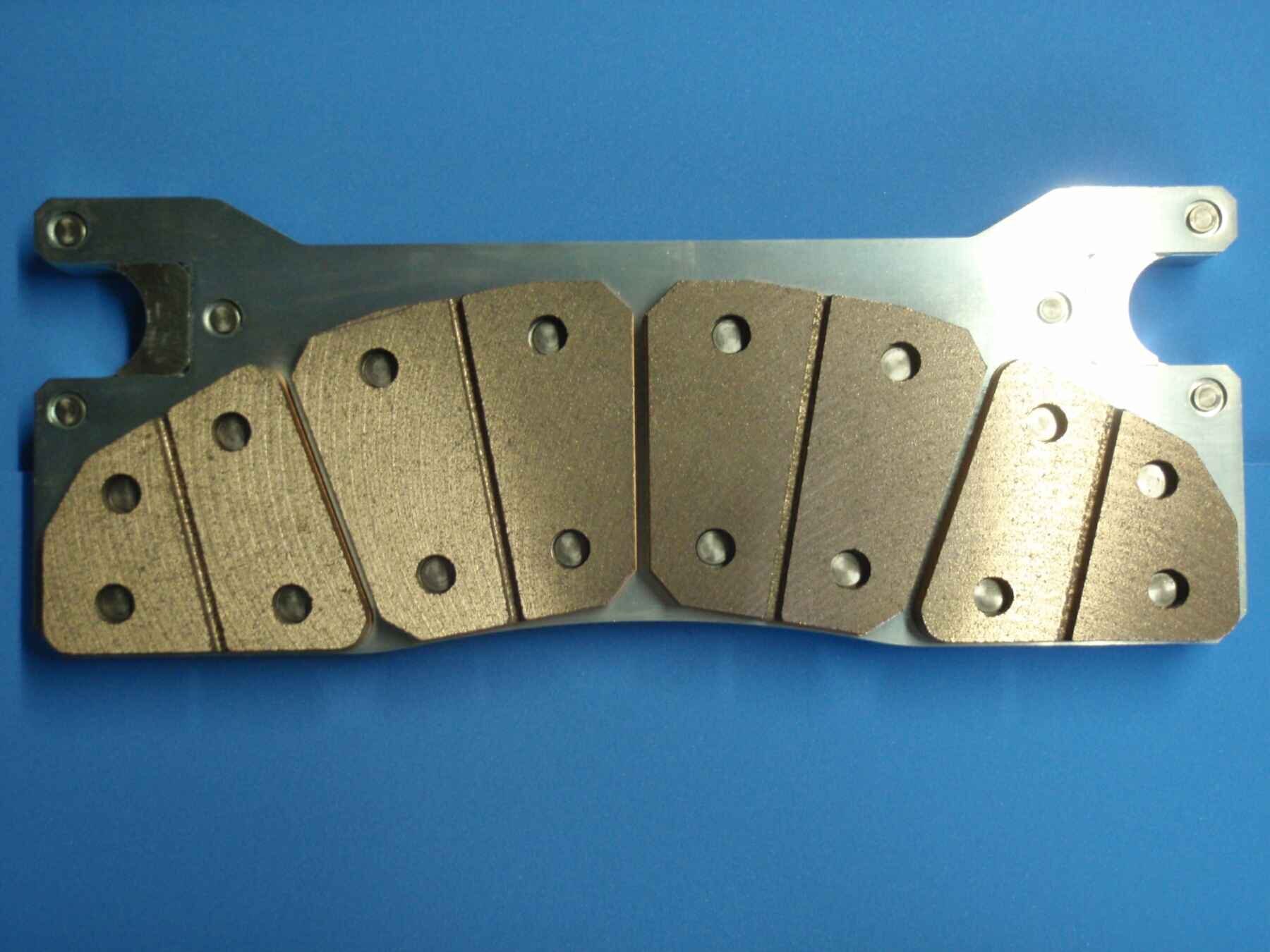
Sintered brake lining for high-speed railway vehicles on conventional lines
The award was given in recognition of the material design that takes into consideration not only brake performance but also ride comfort, its adoption by the railway industry and the potential for future expansion of applications including overseas were widely recognized.
New Product Award, New Design
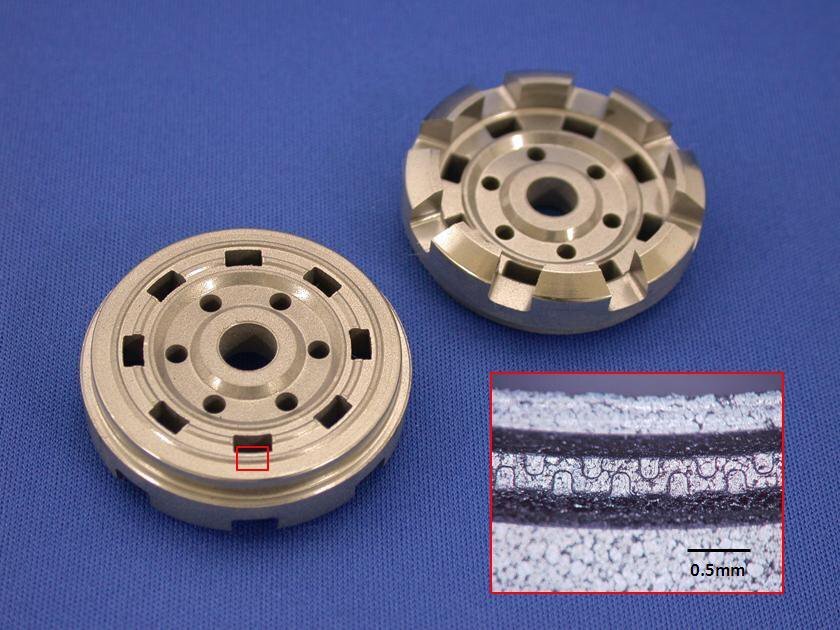
Base valve case that has realized high performance and low price
The development of a technology for transferring minute concave shapes onto high-precision sheet surfaces by sizing in order to provide pores that prevent adsorption was widely recognized for its potential in the future with large mass production volumes and for its contribution to the industry.
New Product Award, Process Development
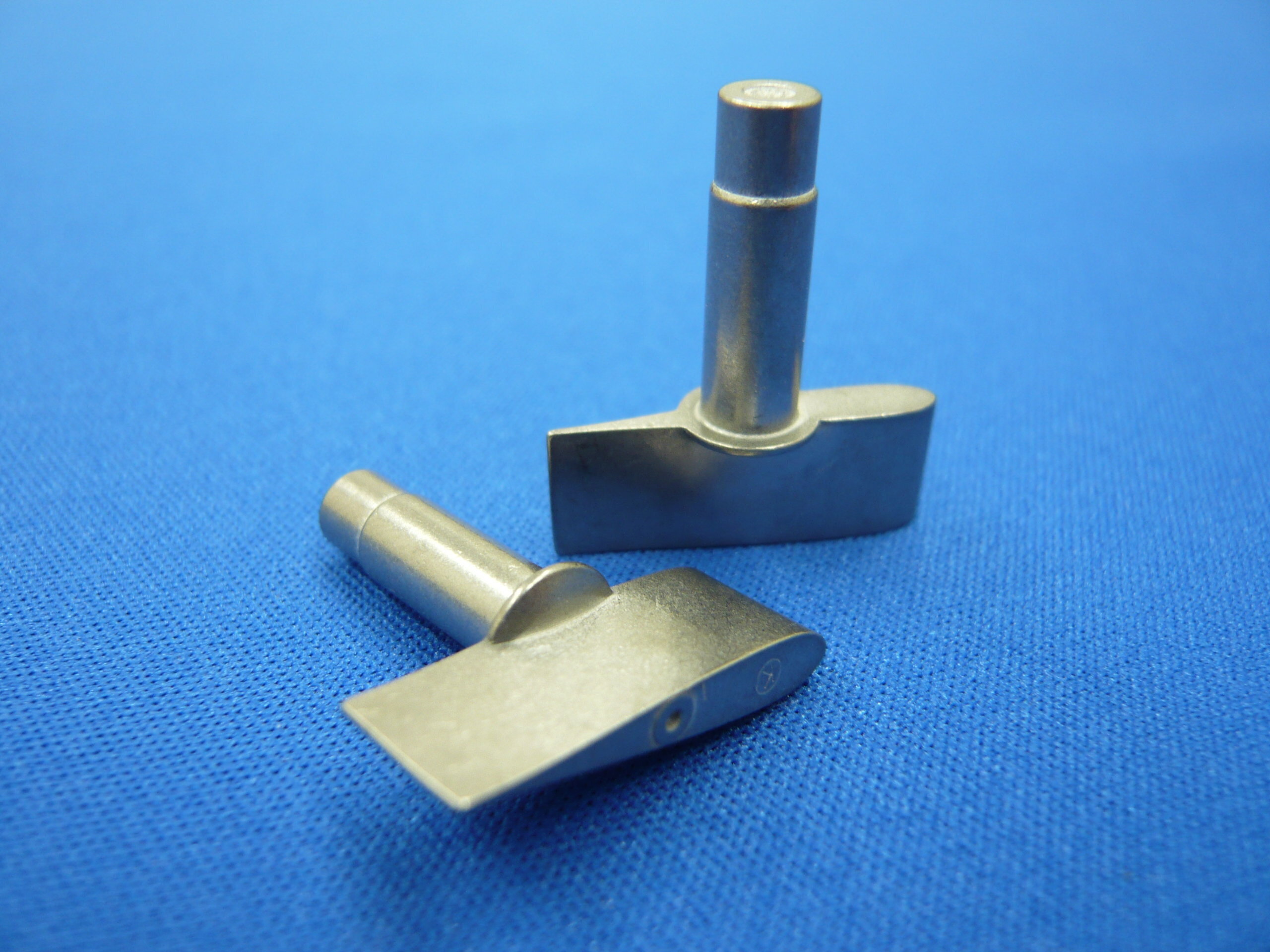
Full net shape manufacturing of MIM parts with high dimensional accuracy
Full net shape manufacturing of MIM parts with high dimensional accuracy was widely recognized as a significant contribution to the industry by increasing the potential in the MIM field.
New Product Award, Process Development
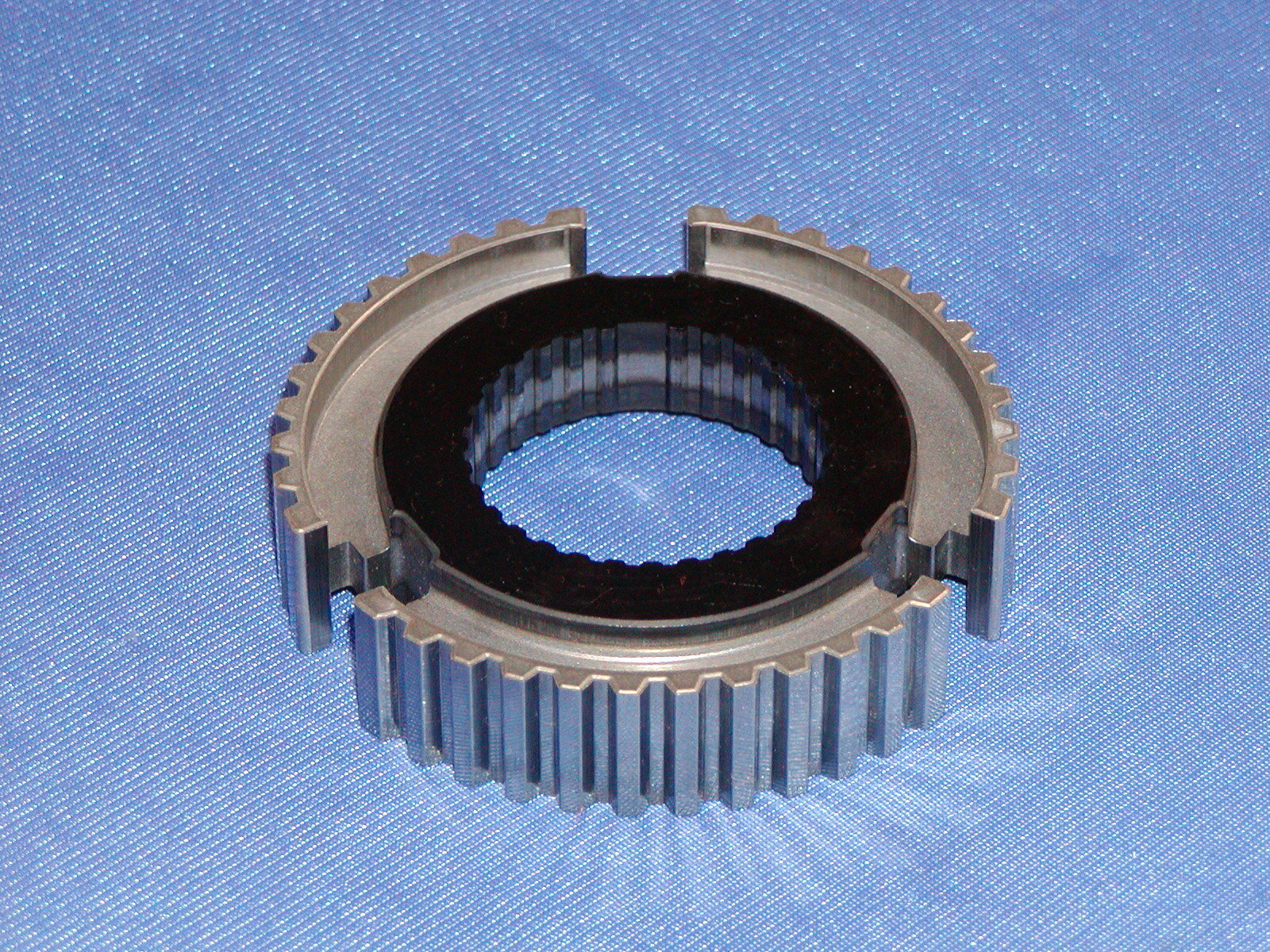
Mass production of high-precision clutch hub that contributes to improved operation feeling
The award was given in recognition of the development of mass production technology for a high-precision sintered clutch hub with minimal cost increase, which significantly contributed to higher performance and improved operation feeling required for automobile manual transmission.
New Product Award, New Design
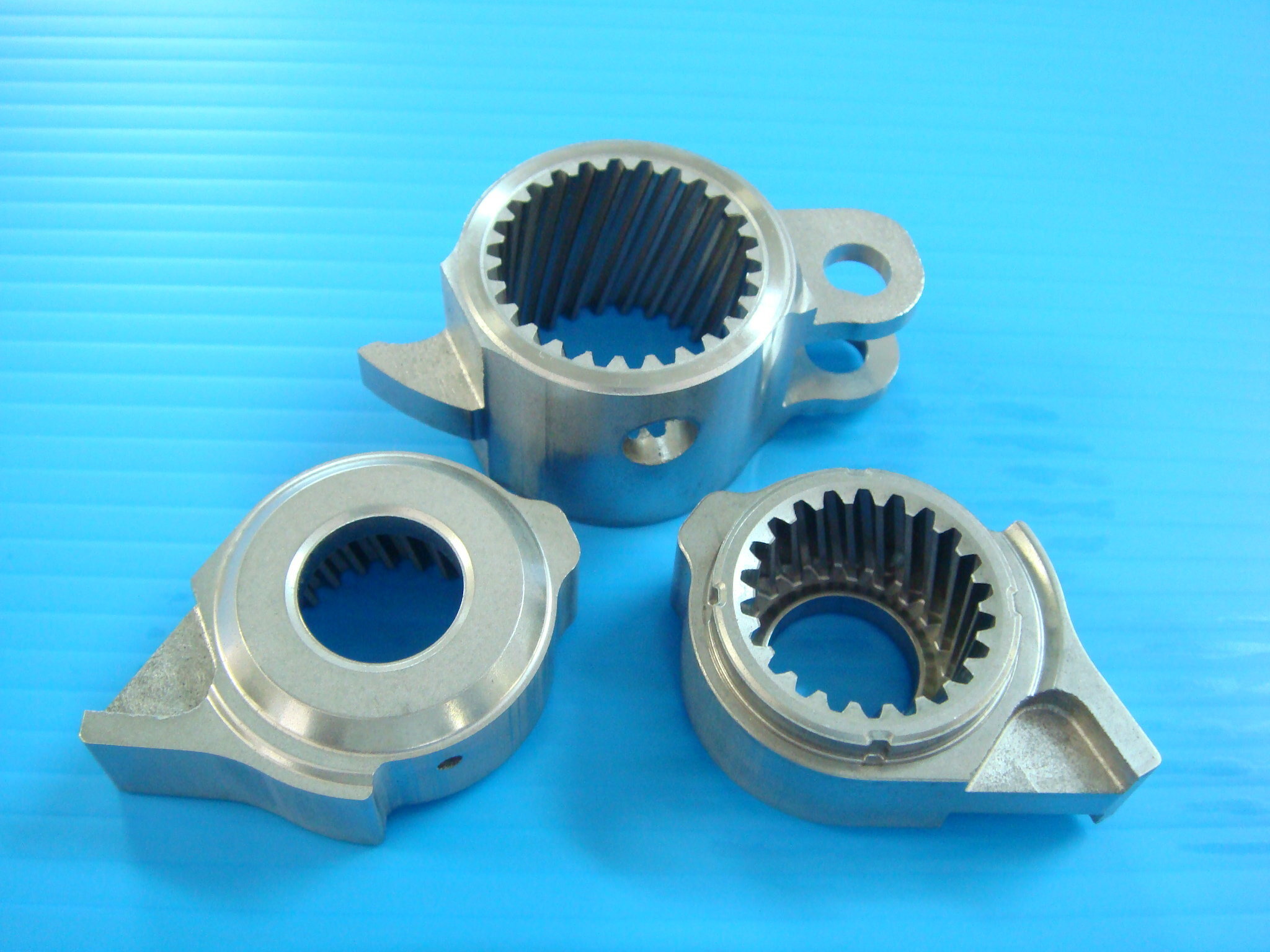
Development of sintered arm for variable valve lift
The award was given in recognition of the technology to combine near-net-shape manufacturing and green machining to produce components with complex outside shapes with inside helical gears, and the technology to develop new sintered mechanical components for the variable valve lift, which will continue to expand in the future.
New Product Award, New Design
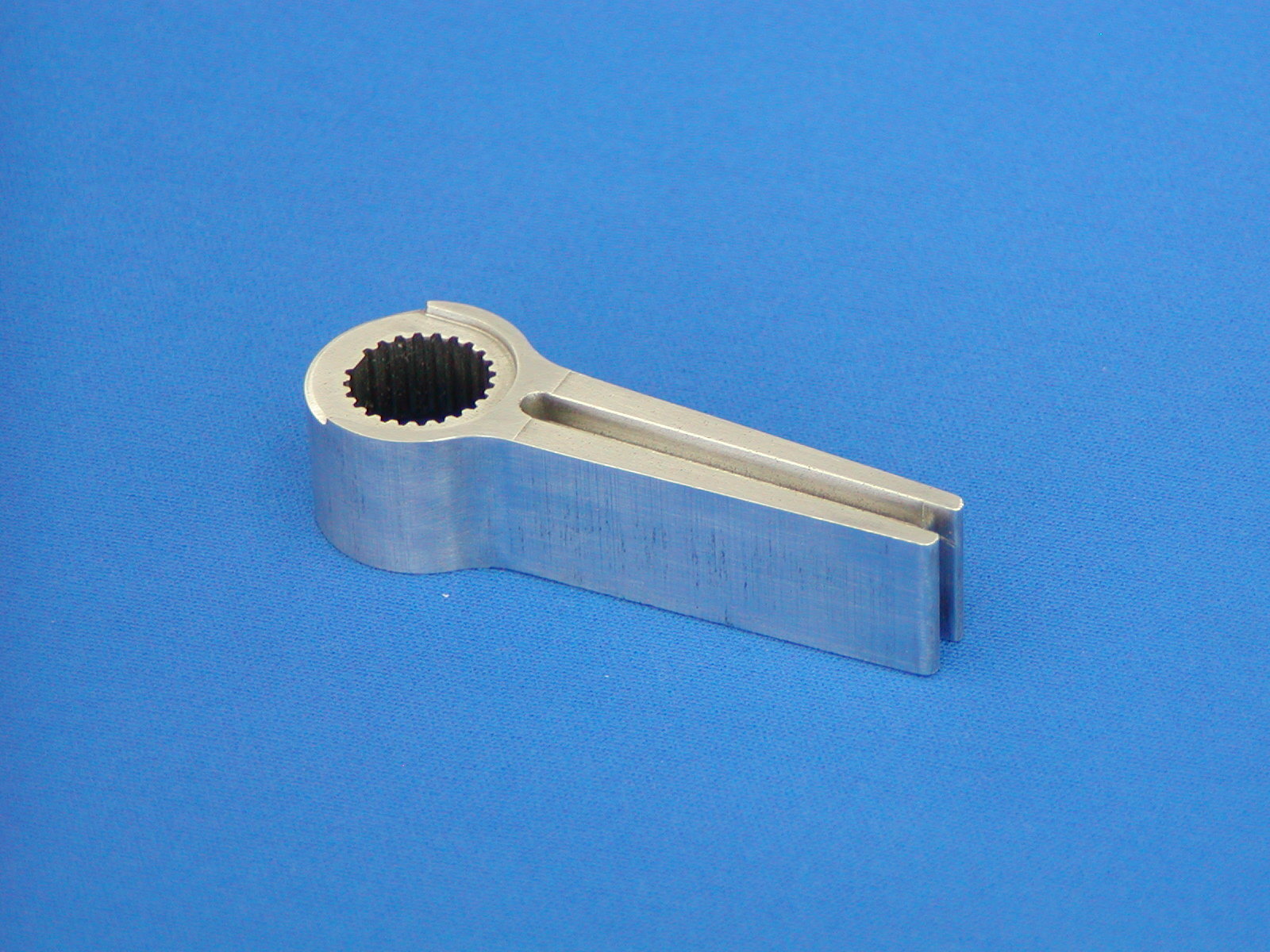
Sintering of aluminum vane for electronically controlled rotary steering damper
The award was given in recognition of the technological expertise to produce vanes with internal splines for the new steering damper system by a press-sinter method using aluminum powder instead of simple shape extrusion method.
Raw Material Award
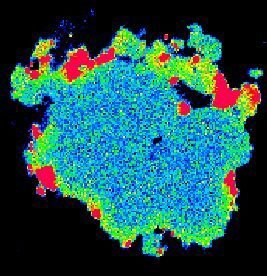
Hybrid type Mo alloy steel powder for high fatigue strength sintered parts
The development of Mo alloy steel powder that achieved high fatigue strength in a general-purpose mesh belt furnace was widely recognized for its contribution to the production of low-cost, high-fatigue strength parts at sintering manufacturers.
Effort Prize
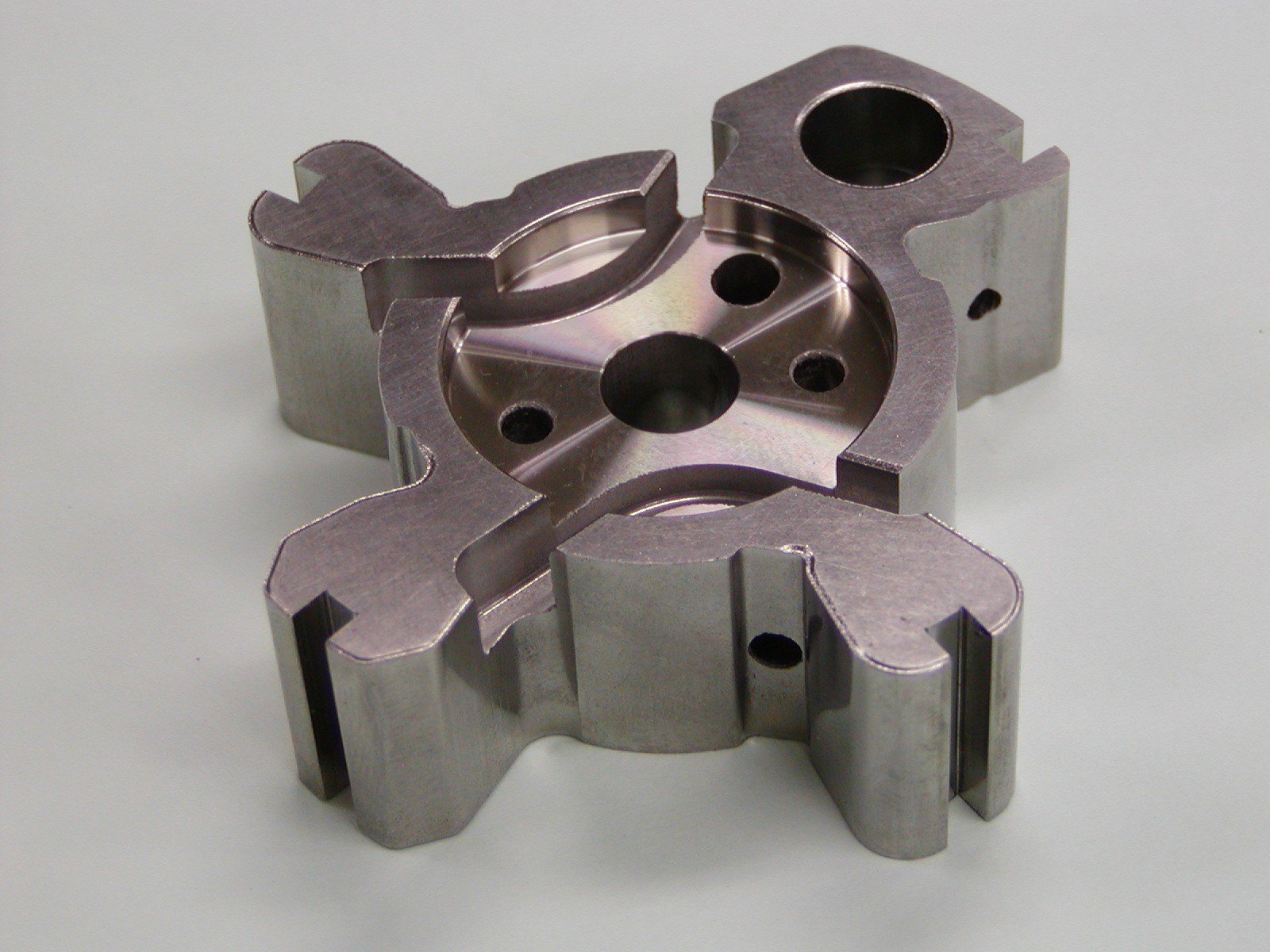
Green machining and sintering of low cost VCT rotor
The application of green machining to hydraulic parts, which must not be contaminated with foreign matter, was widely recognized for ensuring reliability and significantly reducing machining costs, as well as for its ripple effect in expanding the application of green machining in the future.
New Product Award, New Design
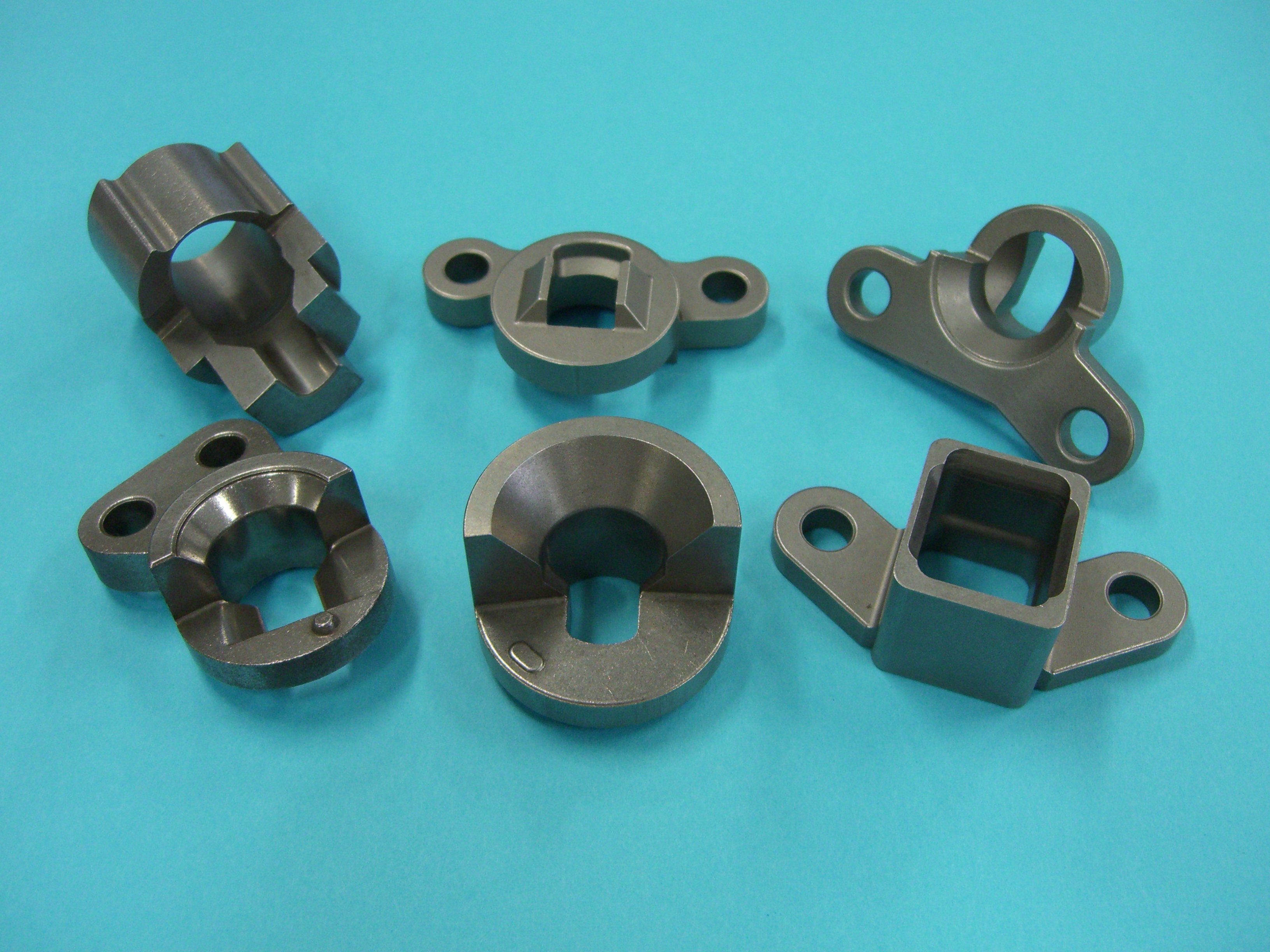
Sintering of AT parts with tapered inner diameter
The award was given in recognition of the technological expertise to manufacture complicated shapes by press compaction and sintering, the versatility of application to similarly shaped products, and its adoption as important automotive safety parts.
New Product Award, New Design
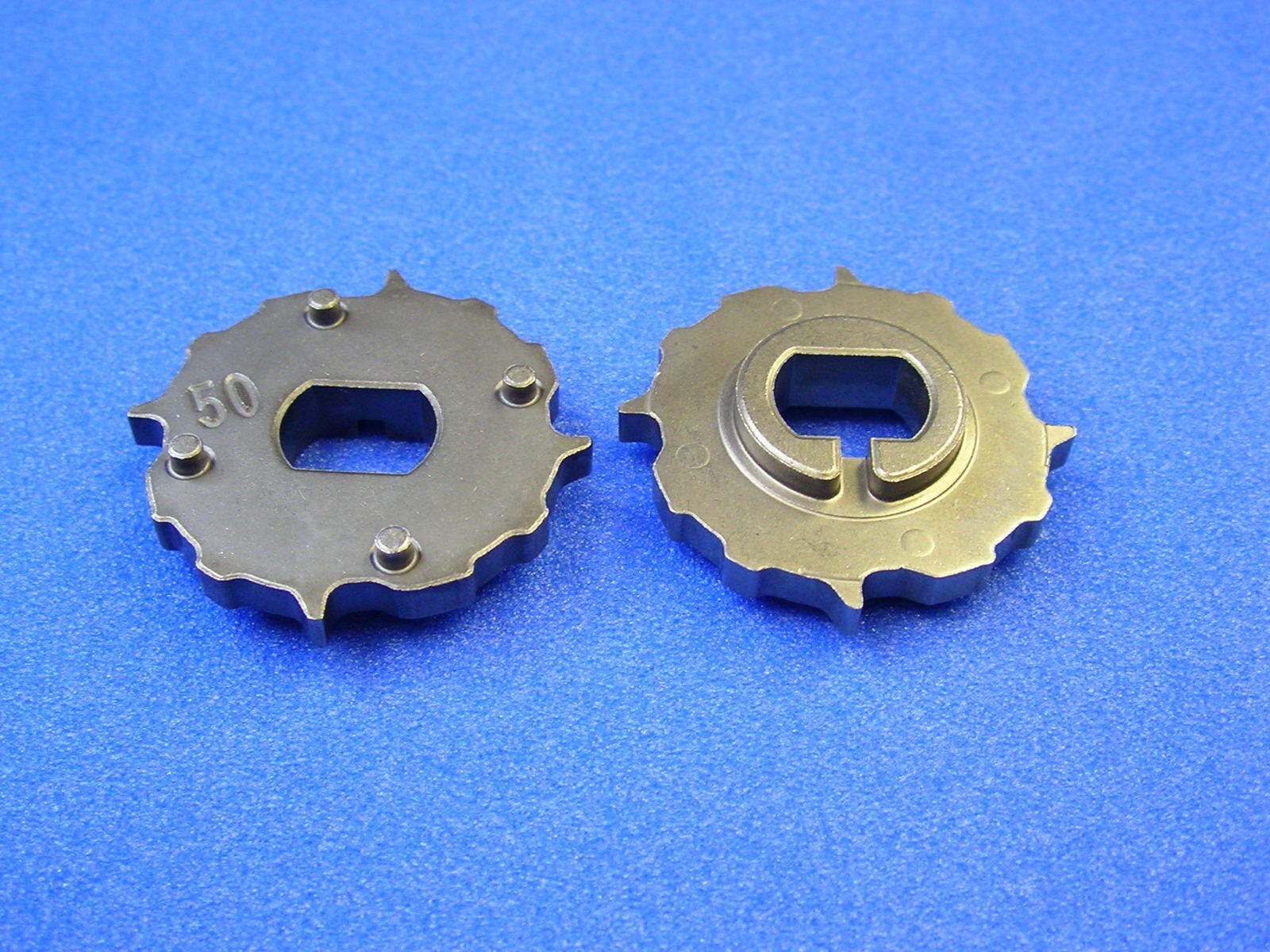
Sintering of the cam for reclining seat
It was widely recognized that the pin part, which is prone to defects during compaction, was mass produced by compaction press, while ensuring and guaranteeing strength.
New Product Award, New Material
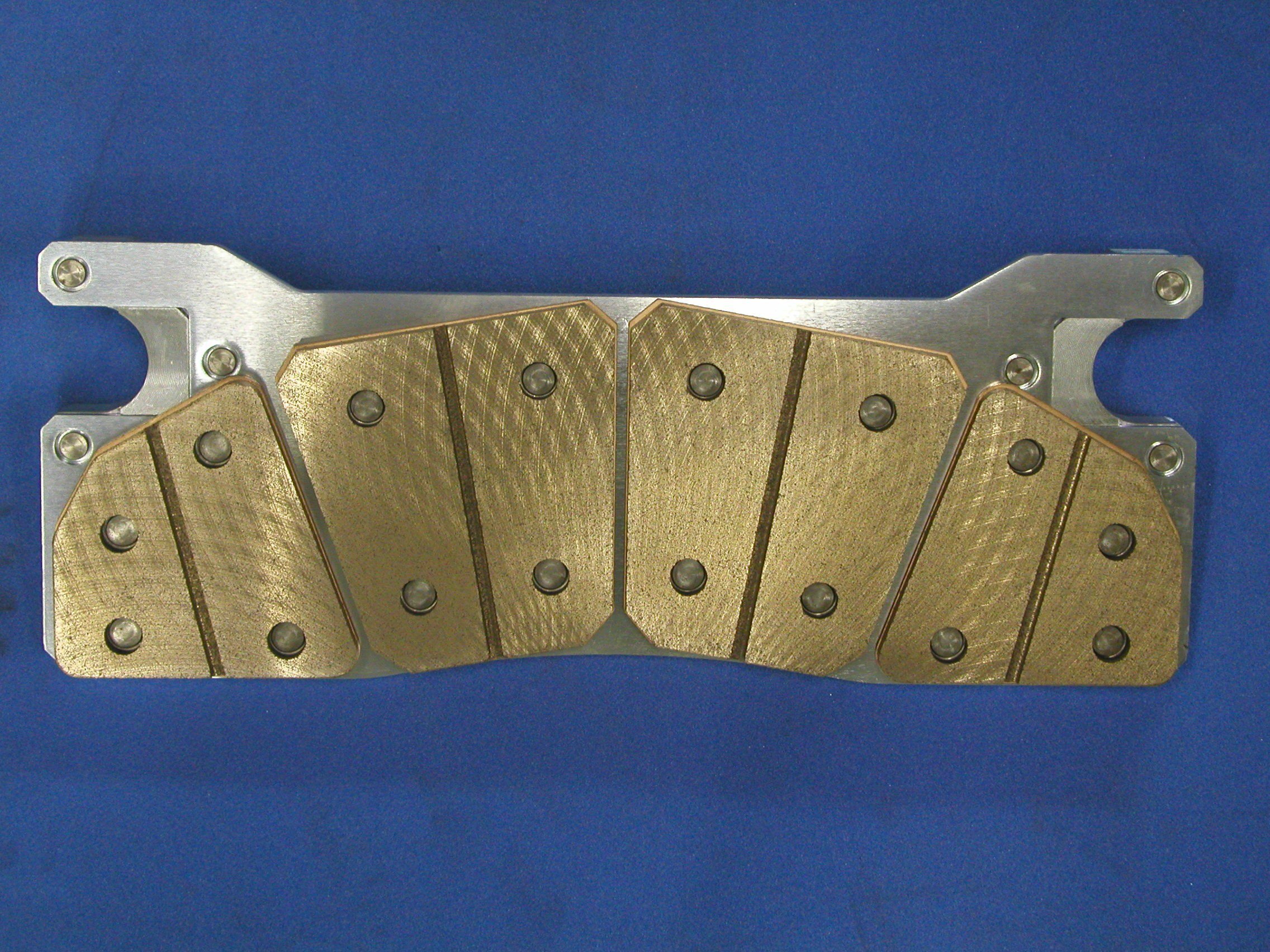
Brake lining for next-generation high-speed vehicles
The key to increasing the speed of railway vehicles is the brake lining. The achievement in practical application of the brake lining product that can handle a maximum speed of 350 km/h was widely recognized.
Effort Prize
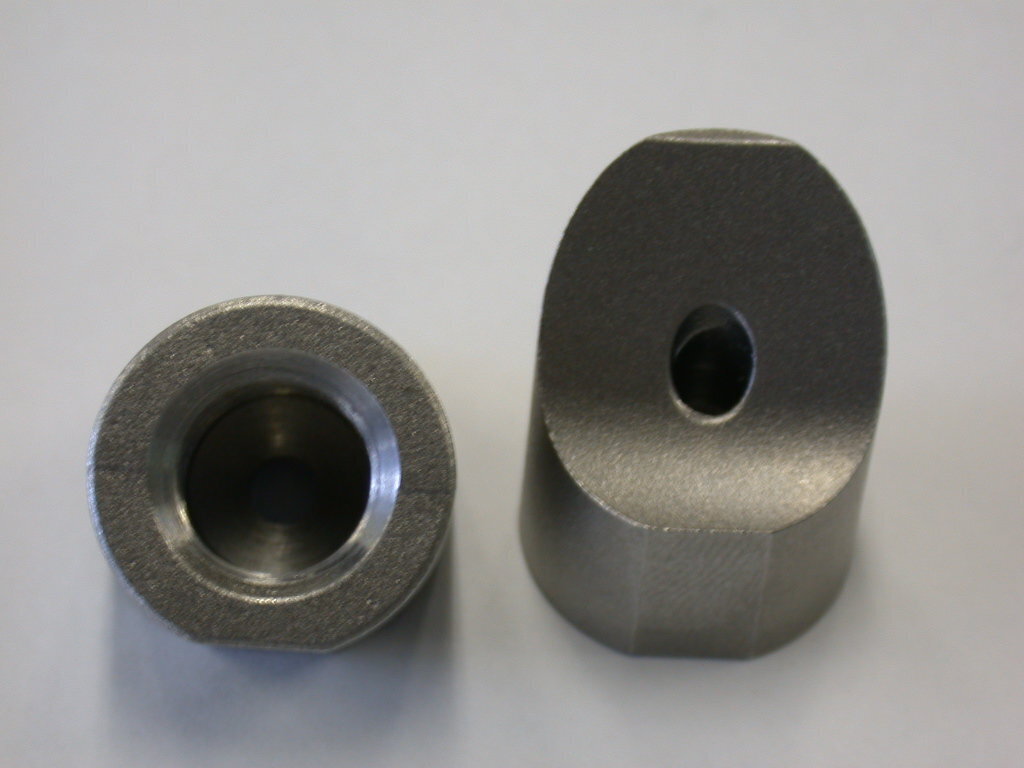
Sintering of exhaust system components with inclined surfaces
The award was given in recognition of the technological expertise to manufacture high-density stainless-steel parts with inclined surfaces by preventing die galling and achieving density balance through ingenuity in the die.
Effort Prize
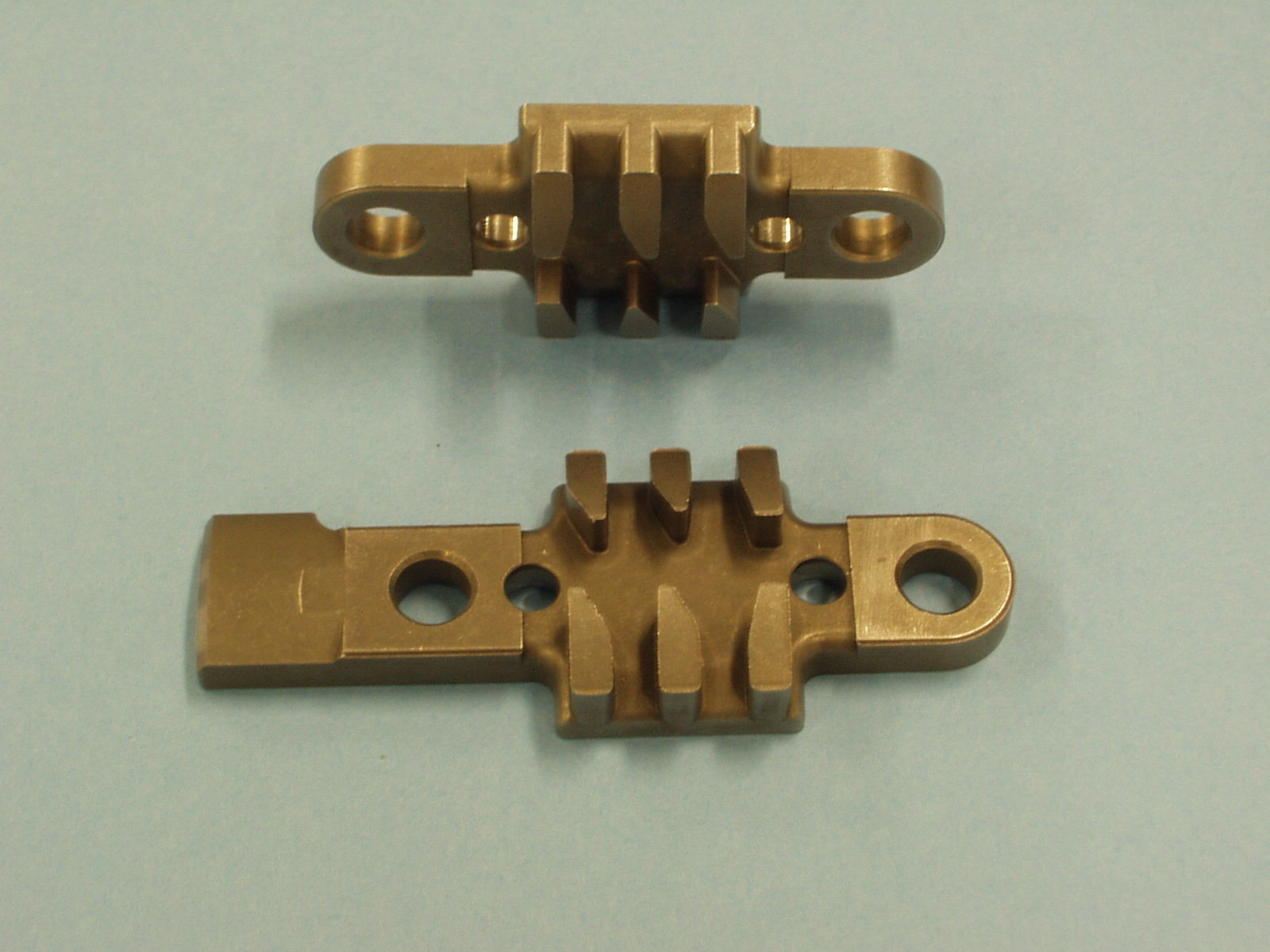
Sintering of transmission parts with multiple protrusions
The award was given in recognition of the technological expertise to manufacture thin-walled parts with protrusions by compaction method, which is usually difficult due to die structure.
New Product Award, Process Development
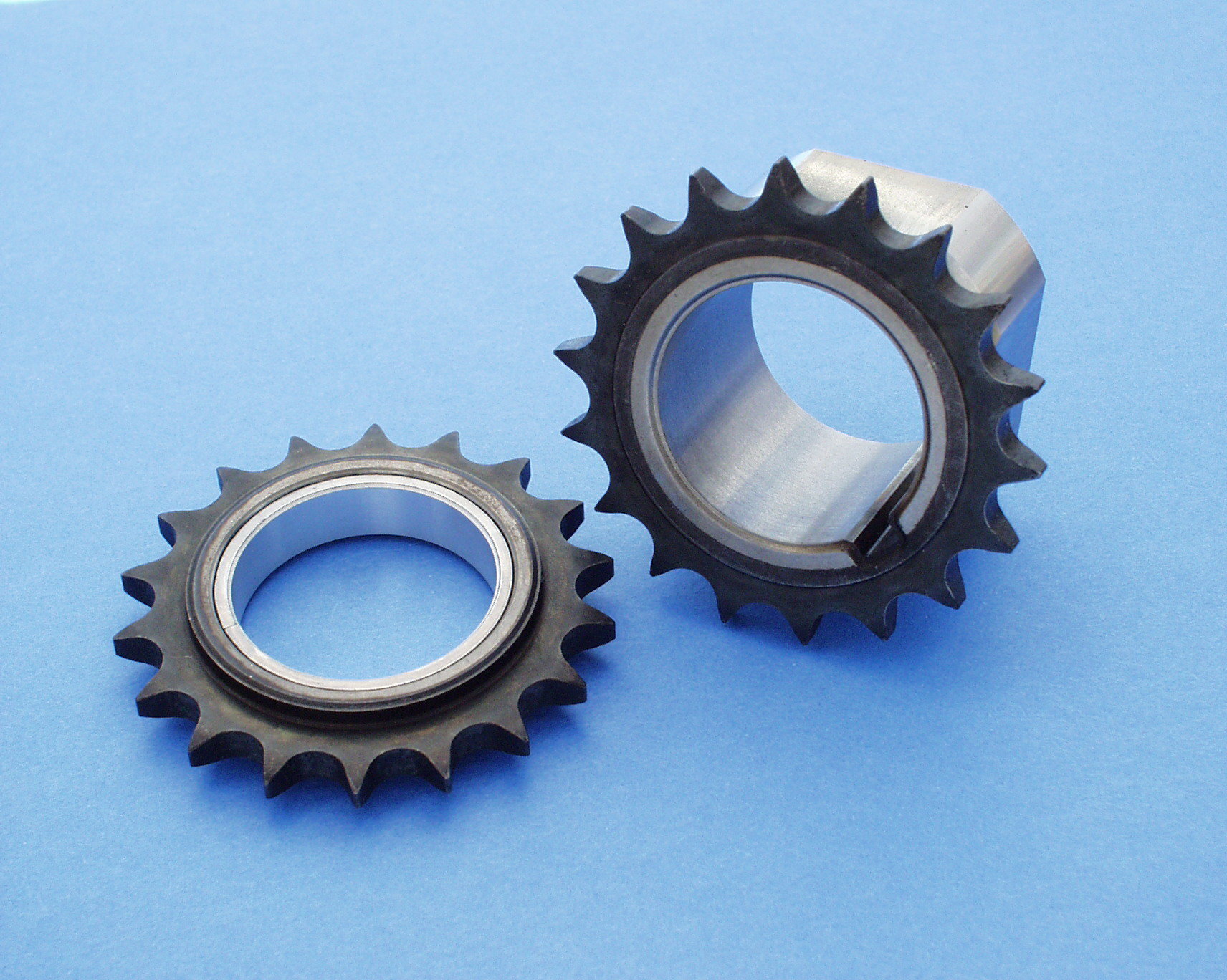
Technology & Development Award from Toyota Motor Corporation
Development of high-strength engine sprocket by warm compaction method with die lubrication
The award was given in recognition of the development of a mass-production technique for high density mechanical structural parts by combining the warm compaction method and original die lubrication method and applying it to complicated shapes. Development of this technique is expected to expand in the future.
Effort Prize
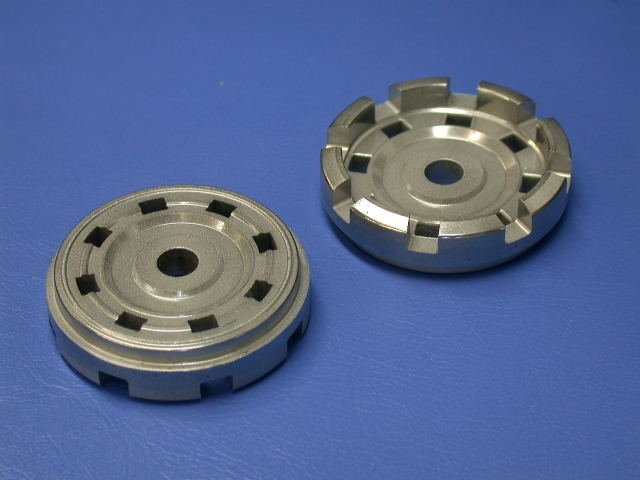
Cost reduction by chamfering outer corners of both end faces of base valve case by using press machine
The award was given in recognition of the cost reduction achieved by applying the highly versatile machining elimination technology to parts with extremely large production volumes.
Grand Prix
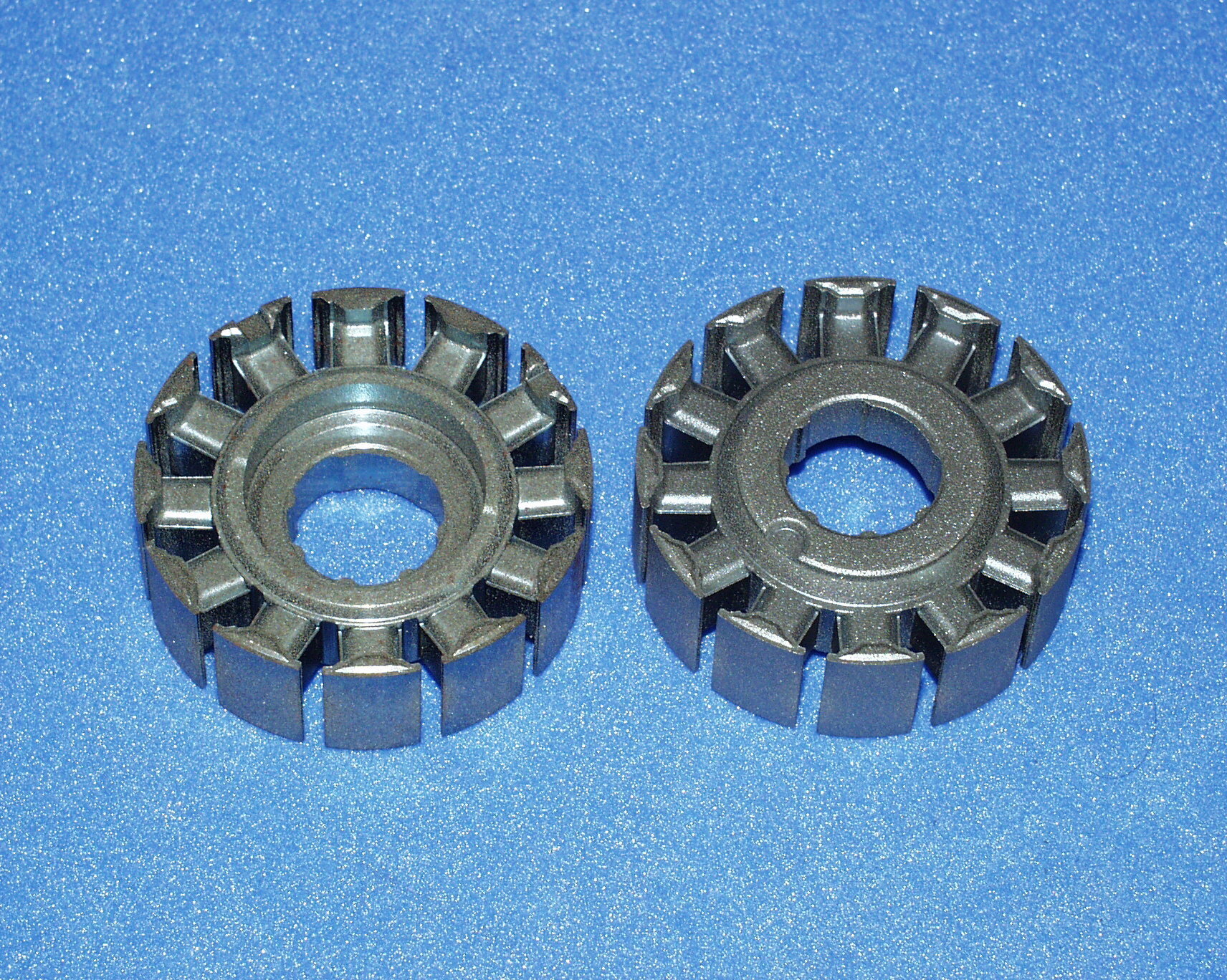
Development of motor core for new ABS (anti-lock braking system)
The award was given in recognition of the first mass production of a three-dimensionally shaped automotive motor core with excellent recyclability that meets users' demands for smaller motors, by taking advantage of the features of powder compaction, as well as the development of the market for soft magnetic parts applications for automobiles, which is expected to expand in the future.
New Product Award, New Design
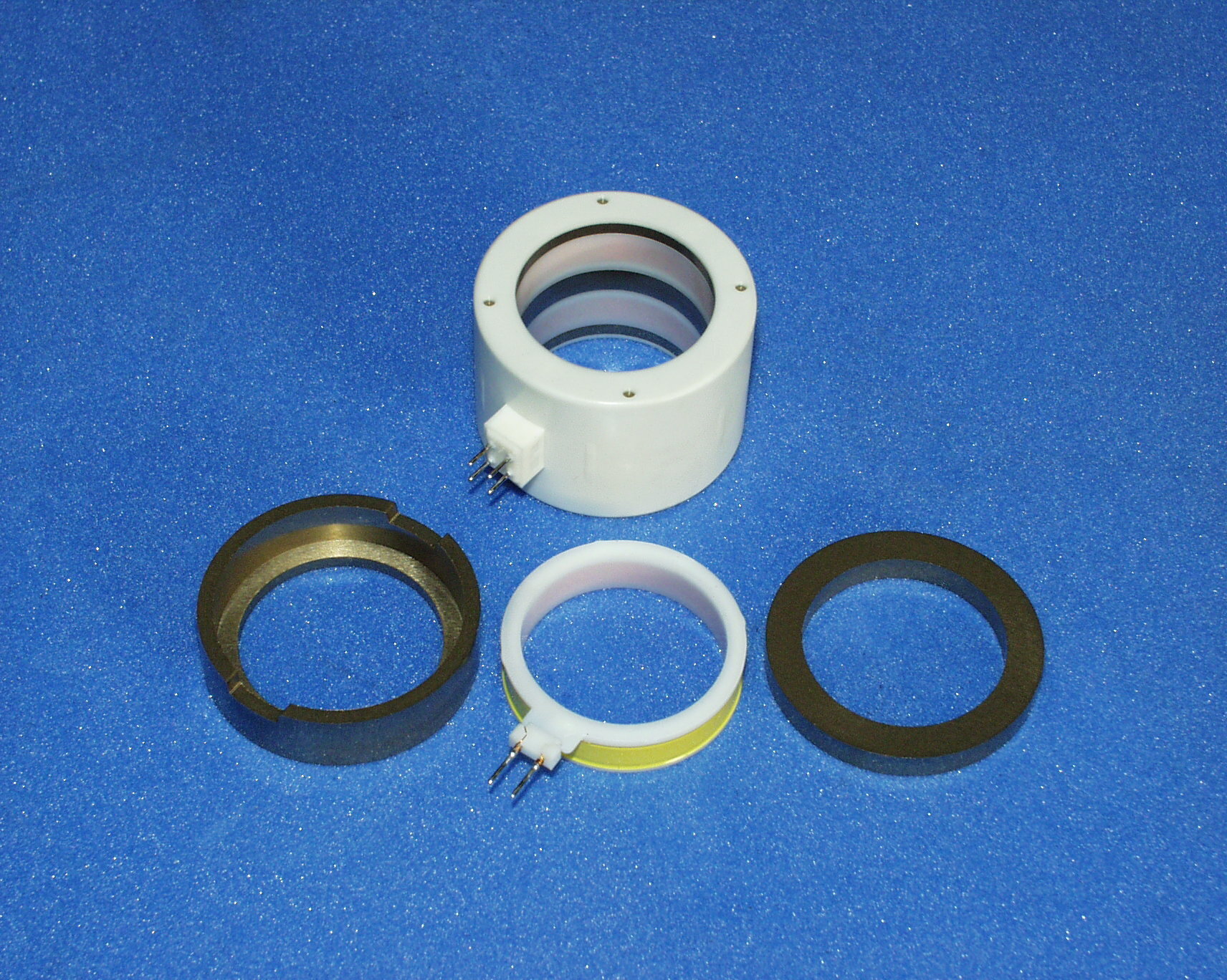
Development of torque sensor for electric power steering using composite soft magnetic material
The award was given in recognition of the technological expertise to produce composites of pressed powder core and resin, which increased the added value of parts, as well as its application in electric power steering parts, for which demand is expected to expand in the future.
Effort Prize
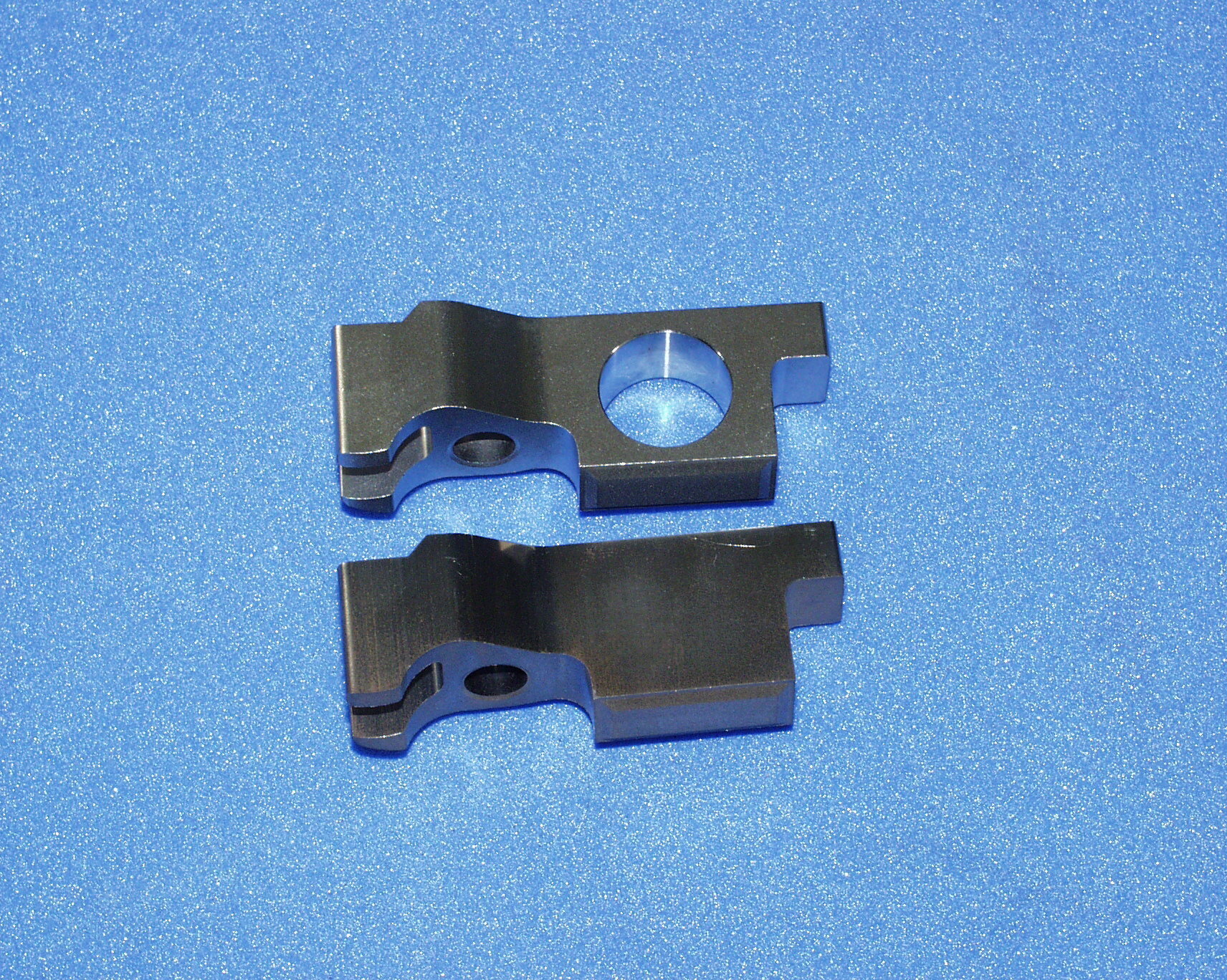
Green machining of clamps and nozzle holders
This award was given in recognition of the practical application of green machining using conventional compacts at the mass production level and its application to automotive parts.
New Product Award, New Design
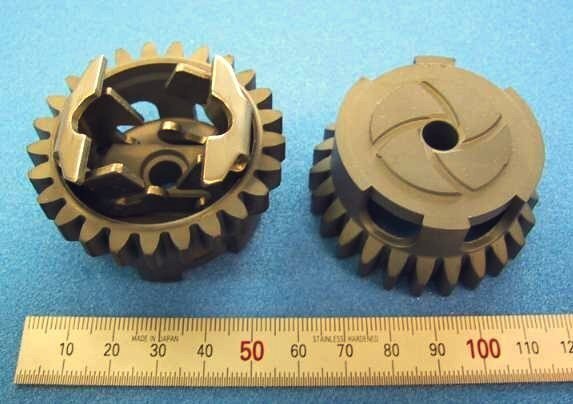
Sintering of governor gear for general-purpose engine
This award was given in recognition of the practical application of a thin-walled, multi-step, complex-shaped product by taking advantage of the merits of CNC press, as well as using multifunctionality achieved by integration as a characteristic of powder metallurgy.
Equipment Development Award
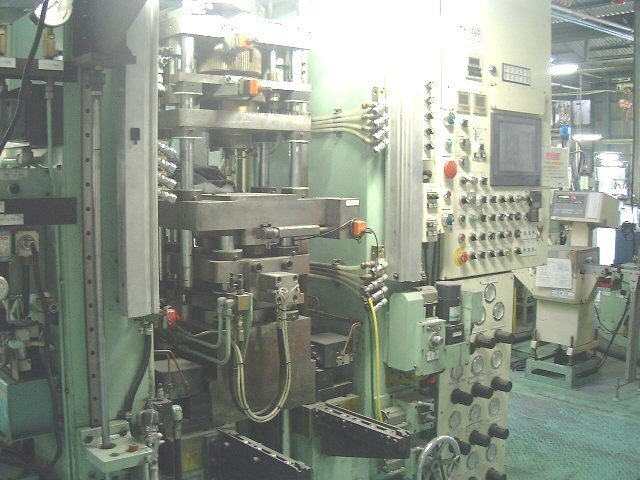
Partial CNC powder compaction press
The award was given in recognition of the versatility of the CNC press, which enables complex shapes of powder metallurgy products with a relatively small capital investment.
The Japan Society of Powder and Powder Metallurgy (JSPM) was founded in May 1958. The JSPM aims to promote and provide cooperation in research on powders and powder metallurgy, and to contribute to the development of science and technology.
See more about the Japan Society of Powder and Powder Metallurgy
Activities of the Japan Society of Powder and Powder Metallurgy
-
Events
The JSPM holds research presentations (annual meetings) twice a year in spring and autumn, as well as lectures and discussion meetings.
In addition, tutorial courses on powder metallurgy offer lectures on the basics of powder metallurgy and new possibilities related to powder metallurgy.
-
Publications
The JSPM publishes the “Journal of the Japan Society of Powder and Powder Metallurgy [Funtai oyobi Funmatsu Yakin]” and academic publications,
and also invites contributions from the general public on special topics.
-
JSPM Awards
The JSPM Awards are given to individuals for outstanding basic research or technological development, and outstanding achievements in the fields of powder and powder metallurgy.
-
Subcommittees
Subcommittee activities are divided into seven subcommittees, such as Fundamental of Powder Metallurgy, Hard Materials, and Magnetic Materials. Each subcommittee holds research discussion meetings to exchange information and discuss recent research results and future prospects.